Functional Treatments
Chemical nickel
Functional Treatments
Chemical nickel
Functional treatments: chemical nickel plating
What is chemical nickel plating?
In electrolytic processes, metal deposition occurs by the passage of current between the cathode (object to be coated) and the anode (inert or source of the metal). In the case of electroless nickel, there is no current flow. Deposition occurs due to the chemical composition of the bath. In fact, the bath contains a reducing agent that, at the proper temperature and on surfaces prepared for the purpose, initiates the nickel reduction reaction, forming the “chemical” nickel deposit, so called precisely because it is initiated and maintained by a series of chemical reactions and temperature.
The fact that the nickel deposit is formed without the passage of electric current offers a number of advantages, dependent mainly on the fact that since there is no electric field conditioning the growth of the deposit, it occurs uniformly. Not only that, the deposit also grows uniformly in undercuts, recesses, holes, and all surfaces wetted by the solution. Nickel in the deposition phase incorporates phosphorus. The amount of phosphorus incorporated determines certain characteristics of the deposit such as hardness and corrosion resistance.
Three types of electroless nickel deposition baths are distinguished:
- high phosphorus
- medium phosphorus
- low phosphorus
In any case, heat treatment at 400°C can be operated to bring the hardness up to 900 to 950 Hv from, on average, 450 to 500Hv.
To sum up, the special characteristics of electroless nickel are:
- uniformity of thickness
- low coefficient of friction
- Hardness that with heat treatment can reach around 900Hv
- Deposition in all wettable recesses from the deposition bath
- good corrosion resistance
Deposition of electroless nickel can be done by frame, while small parts can be processed by rotobarrel. Tobaldini performs electroless nickel plating on iron, stainless steel, brass, aluminum, etc.
How does the process take place?
The oxide that is formed is not due to material input but to a transformation of the original surface of the object. The aluminum surface undergoing anodizing is progressively oxidized from the outside of the surface progressing inward. The ‘oxide that is formed has a larger volume than the original metal (aluminum) so that apparently, from a dimensional point of view, it seems away is a material contribution, in reality the thickness of oxide partly “penetrates” into the metal partly “grows” outward. In practice for a thickness of e.g. 10 microns, 5 microns penetrated and 5 microns expanded so the geometric increase amounts to 5 microns. Note that, on a diameter, the 10-micron thickness produces an increase in diameter of 10 microns, not 20.
Oxide also tends to form fairly uniformly in recesses, undercuts, and inside pipes. The structure of the oxide is very similar to the “honeycomb” structure with vertical tubules with respect to the thickness formed. These tubules are much less than a micron in diameter, but particular dyes can penetrate them, being able to impart a wide variety of colorations to the oxide layer. Following the formation of the oxide layer and, eventual staining, a pore-closing operation is performed in order to ensure compactness and corrosion resistance. This operation is called fixing and can be done cold or hot. in any case, the pores are closed; however, it turns out to be safer to heat fix especially for colored oxide layers.
Functional treatments: chemical nickel plating
What is chemical nickel plating?
In electrolytic processes, metal deposition occurs by the passage of current between the cathode (object to be coated) and the anode (inert or source of the metal). In the case of electroless nickel, there is no current flow. Deposition occurs due to the chemical composition of the bath. In fact, the bath contains a reducing agent that, at the proper temperature and on surfaces prepared for the purpose, initiates the nickel reduction reaction, forming the “chemical” nickel deposit, so called precisely because it is initiated and maintained by a series of chemical reactions and temperature.
The fact that the nickel deposit is formed without the passage of electric current offers a number of advantages, dependent mainly on the fact that since there is no electric field conditioning the growth of the deposit, it occurs uniformly. Not only that, the deposit also grows uniformly in undercuts, recesses, holes, and all surfaces wetted by the solution. Nickel in the deposition phase incorporates phosphorus. The amount of phosphorus incorporated determines certain characteristics of the deposit such as hardness and corrosion resistance.
Three types of electroless nickel deposition baths are distinguished:
- high phosphorus
- medium phosphorus
- low phosphorus
In any case, heat treatment at 400°C can be operated to bring the hardness up to 900 to 950 Hv from, on average, 450 to 500Hv.
To sum up, the special characteristics of electroless nickel are:
- uniformity of thickness
- low coefficient of friction
- Hardness that with heat treatment can reach around 900Hv
- Deposition in all wettable recesses from the deposition bath
- good corrosion resistance
Deposition of electroless nickel can be done by frame, while small parts can be processed by rotobarrel. Tobaldini performs electroless nickel plating on iron, stainless steel, brass, aluminum, etc.
How does the process take place?
The oxide that is formed is not due to material input but to a transformation of the original surface of the object. The aluminum surface undergoing anodizing is progressively oxidized from the outside of the surface progressing inward. The ‘oxide that is formed has a larger volume than the original metal (aluminum) so that apparently, from a dimensional point of view, it seems away is a material contribution, in reality the thickness of oxide partly “penetrates” into the metal partly “grows” outward. In practice for a thickness of e.g. 10 microns, 5 microns penetrated and 5 microns expanded so the geometric increase amounts to 5 microns. Note that, on a diameter, the 10-micron thickness produces an increase in diameter of 10 microns, not 20.
Oxide also tends to form fairly uniformly in recesses, undercuts, and inside pipes. The structure of the oxide is very similar to the “honeycomb” structure with vertical tubules with respect to the thickness formed. These tubules are much less than a micron in diameter, but particular dyes can penetrate them, being able to impart a wide variety of colorations to the oxide layer. Following the formation of the oxide layer and, eventual staining, a pore-closing operation is performed in order to ensure compactness and corrosion resistance. This operation is called fixing and can be done cold or hot. in any case, the pores are closed; however, it turns out to be safer to heat fix especially for colored oxide layers.
Treatable materials
- Stainless steel, AISI 316, AISI 304, AISI 303,
- Carbon steel, iron, C40, C45, AVP, AVZ
- Aluminum, cast aluminum, 2011, 11S, 6060, 6082, 7075, Anticorodal, Ergal
- Brass
- Copper
- Sintered
- Zama
Regulations
- UNI ISO 4527
Possible finishes
- White passivation (chrome 3)
- High strength passivation (chrome 3)
- Black passivation (chrome 3)
Maximum treatable size
2700x500x1200 mm
Treatable materials
- Stainless steel, AISI 316, AISI 304, AISI 303,
- Carbon steel, iron, C40, C45, AVP, AVZ
- Aluminum, cast aluminum, 2011, 11S, 6060, 6082, 7075, Anticorodal, Ergal
- Brass
- Copper
- Sintered
- Zama
Possible finishes
- White passivation (chrome 3)
- High strength passivation (chrome 3)
- Black passivation (chrome 3)
Regulations
- UNI ISO 4527
Maximum treatable size
2700x500x1200 mm
Sectors
implementing
implementing
Application areas
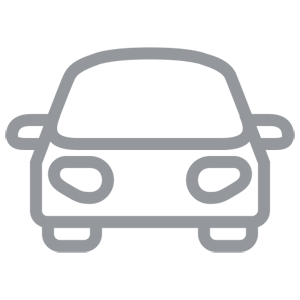
Automotive
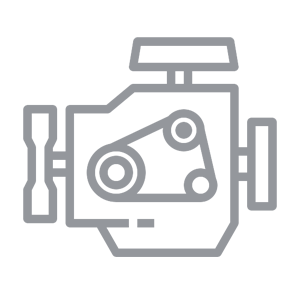
Mechanics
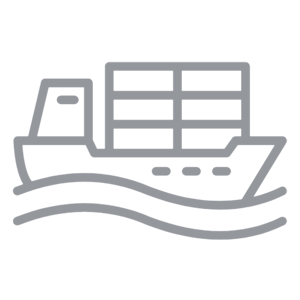
Naval/nautical
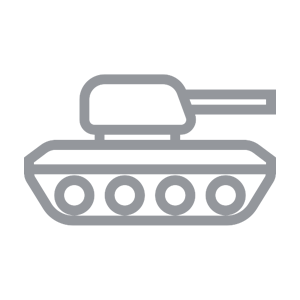
Military
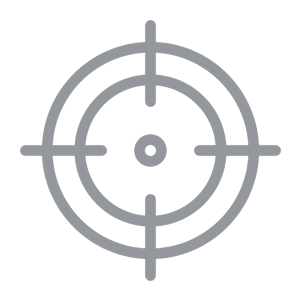
Precision systems
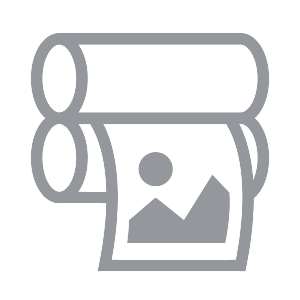
Paint or printing rollers
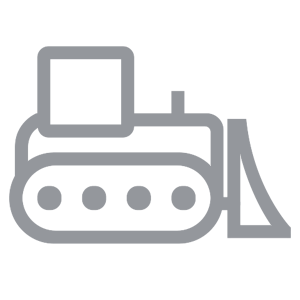
Earthmoving
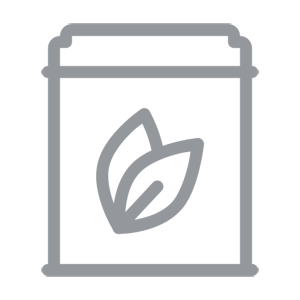