Trattamenti funzionali
Nichel chimico
Trattamenti funzionali
Nichel chimico
Trattamenti funzionali: la nichelatura chimica
Cos’è la nichelatura chimica?
Nei processi elettrolitici, il deposito di metallo avviene tramite il passaggio di corrente fra il catodo (oggetto da rivestire) e l’anodo (inerte o fonte del metallo). Nel caso del nichel chimico, non vi è alcun flusso di corrente. Il deposito avviene grazie alla composizione chimica del bagno. Il bagno contiene infatti un riducente che, alla adeguata temperatura e su superfici preparate allo scopo, avvia la reazione di riduzione del nichel, formando il deposito di nichel “chimico”, chiamato così appunto perché avviato e mantenuto da una serie di reazioni chimiche e dalla temperatura.
Il fatto che si formi il deposito di nichel senza il passaggio di corrente elettrica offre una serie di vantaggi, dipendenti soprattutto dal fatto che non essendoci un campo elettrico che condiziona la crescita del deposito, questo avviene in modo uniforme. Non solo, il deposito si accresce uniforme anche nei sottosquadra, nei recessi, nei fori, in tutte le superfici bagnate dalla soluzione. Il nichel nella fase di deposizione ingloba fosforo. La quantità di fosforo inglobato determina alcune caratteristiche del deposito quali la durezza e la resistenza alla corrosione.
Si distinguono tre tipi di bagni per la deposizione di nichel chimico:
- ad alto fosforo
- a medio fosforo
- a basso fosforo
In ogni caso è possibile operare un trattamento termico a 400°C per portare la durezza fino a 900 – 950 Hv a partire, mediamente da 450 – 500Hv.
Riassumendo, le caratteristiche peculiari del nichel chimico sono:
- uniformità dello spessore
- basso coefficiente di attrito
- durezza che con trattamento termico può arrivare intorno ai 900Hv
- deposito in tutti i recessi bagnabili dal bagno di deposizione
- buona resistenza alla corrosione
Il deposito di nichel chimico può essere fatto a telaio, mentre la minuteria può essere trattata a rotobarile. La Tobaldini esegue riporti di nichel chimico su ferro, acciaio inox, ottone, alluminio ecc.
Come avviene il processo?
L’ossido che si forma non è dovuto ad un apporto di materiale ma ad una trasformazione della superficie originale dell’oggetto. La superficie di alluminio sottoposta ad anodizzazione viene ossidata progressivamente dall’esterno della superficie progredendo verso l’interno. L’ ossido che si forma ha un volume maggiore del metallo (alluminio) originario per cui apparentemente, dal punto di vista dimensionale, sembra via sia un apporto di materiale, in realtà lo spessore di ossido in parte “penetra” nel metallo in parte “cresce” verso l’esterno. In pratica per uno spessore di es. 10 micron, 5 micron sono penetrati e 5 micron si sono espansi per cui l’aumento geometrico ammonta a 5 micron. Da notare che, su un diametro, lo spessore di 10 micron produce un aumento del diametro pari a 10 micron e non 20.
L’ossido tende a formarsi abbastanza uniformemente anche nei recessi, nei sottosquadra, all’interno di tubi. La struttura dell’ossido è molto simile alla struttura del “nido d’ape” con tubuli verticali rispetto allo spessore formato. Questi tubuli hanno un diametro molto inferiore al micron, ma particolari coloranti vi possono penetrare, potendo conferire allo strato di ossido una grande varietà di colorazioni. Successivamente alla formazione dello strato di ossido e, alla eventuale colorazione, viene eseguita una operazione di chiusura dei pori al fine di garantire compattezza e resistenza alla corrosione. Questa operazione prende il nome di fissaggio e può avvenire a freddo o a caldo. in ogni caso i pori vengono chiusi, risulta tuttavia più sicura l’operazione di fissaggio a caldo soprattutto per gli strati di ossido colorato.
Trattamenti funzionali: la nichelatura chimica
Cos’è la nichelatura chimica?
Nei processi elettrolitici, il deposito di metallo avviene tramite il passaggio di corrente fra il catodo (oggetto da rivestire) e l’anodo (inerte o fonte del metallo). Nel caso del nichel chimico, non vi è alcun flusso di corrente. Il deposito avviene grazie alla composizione chimica del bagno. Il bagno contiene infatti un riducente che, alla adeguata temperatura e su superfici preparate allo scopo, avvia la reazione di riduzione del nichel, formando il deposito di nichel “chimico”, chiamato così appunto perché avviato e mantenuto da una serie di reazioni chimiche e dalla temperatura.
Il fatto che si formi il deposito di nichel senza il passaggio di corrente elettrica offre una serie di vantaggi, dipendenti soprattutto dal fatto che non essendoci un campo elettrico che condiziona la crescita del deposito, questo avviene in modo uniforme. Non solo, il deposito si accresce uniforme anche nei sottosquadra, nei recessi, nei fori, in tutte le superfici bagnate dalla soluzione. Il nichel nella fase di deposizione ingloba fosforo. La quantità di fosforo inglobato determina alcune caratteristiche del deposito quali la durezza e la resistenza alla corrosione.
Si distinguono tre tipi di bagni per la deposizione di nichel chimico:
- ad alto fosforo
- a medio fosforo
- a basso fosforo
In ogni caso è possibile operare un trattamento termico a 400°C per portare la durezza fino a 900 – 950 Hv a partire, mediamente da 450 – 500Hv.
Riassumendo, le caratteristiche peculiari del nichel chimico sono:
- uniformità dello spessore
- basso coefficiente di attrito
- durezza che con trattamento termico può arrivare intorno ai 900Hv
- deposito in tutti i recessi bagnabili dal bagno di deposizione
- buona resistenza alla corrosione
Il deposito di nichel chimico può essere fatto a telaio, mentre la minuteria può essere trattata a rotobarile. La Tobaldini esegue riporti di nichel chimico su ferro, acciaio inox, ottone, alluminio ecc.
Come avviene il processo?
L’ossido che si forma non è dovuto ad un apporto di materiale ma ad una trasformazione della superficie originale dell’oggetto. La superficie di alluminio sottoposta ad anodizzazione viene ossidata progressivamente dall’esterno della superficie progredendo verso l’interno. L’ ossido che si forma ha un volume maggiore del metallo (alluminio) originario per cui apparentemente, dal punto di vista dimensionale, sembra via sia un apporto di materiale, in realtà lo spessore di ossido in parte “penetra” nel metallo in parte “cresce” verso l’esterno. In pratica per uno spessore di es. 10 micron, 5 micron sono penetrati e 5 micron si sono espansi per cui l’aumento geometrico ammonta a 5 micron. Da notare che, su un diametro, lo spessore di 10 micron produce un aumento del diametro pari a 10 micron e non 20.
L’ossido tende a formarsi abbastanza uniformemente anche nei recessi, nei sottosquadra, all’interno di tubi. La struttura dell’ossido è molto simile alla struttura del “nido d’ape” con tubuli verticali rispetto allo spessore formato. Questi tubuli hanno un diametro molto inferiore al micron, ma particolari coloranti vi possono penetrare, potendo conferire allo strato di ossido una grande varietà di colorazioni. Successivamente alla formazione dello strato di ossido e, alla eventuale colorazione, viene eseguita una operazione di chiusura dei pori al fine di garantire compattezza e resistenza alla corrosione. Questa operazione prende il nome di fissaggio e può avvenire a freddo o a caldo. in ogni caso i pori vengono chiusi, risulta tuttavia più sicura l’operazione di fissaggio a caldo soprattutto per gli strati di ossido colorato.
Materiali trattabili
- Acciaio inox, AISI 316, AISI 304, AISI 303,
- Acciaio al carbonio, ferro, C40, C45, AVP, AVZ
- Alluminio, alluminio pressofuso, 2011, 11S, 6060, 6082, 7075, Anticorodal, Ergal
- Ottone
- Rame
- Sinterizzati
- Zama
Normative
- UNI ISO 4527
Possibili finiture
- Passivazione bianca (cromo 3)
- Passivazione alta resistenza (cromo 3)
- Passivazione nera (cromo 3)
Dimensioni massime trattabili
2700x500x1200 mm
Materiali trattabili
- Acciaio inox, AISI 316, AISI 304, AISI 303,
- Acciaio al carbonio, ferro, C40, C45, AVP, AVZ
- Alluminio, alluminio pressofuso, 2011, 11S, 6060, 6082, 7075, Anticorodal, Ergal
- Ottone
- Rame
- Sinterizzati
- Zama
Possibili finiture
- Passivazione bianca (cromo 3)
- Passivazione alta resistenza (cromo 3)
- Passivazione nera (cromo 3)
Normative
- UNI ISO 4527
Dimensioni massime trattabili
2700x500x1200 mm
Settori
d'applicazione
d'applicazione
Settori d'applicazione
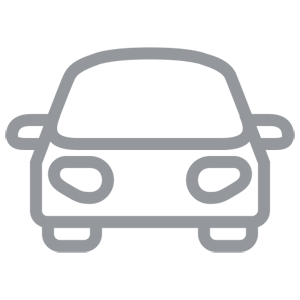
Automotive
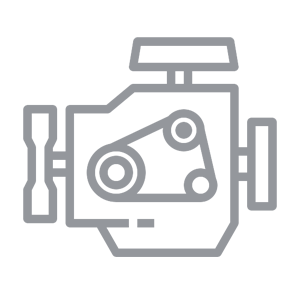
Meccanica
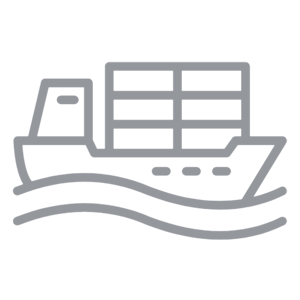
Navale / nautico
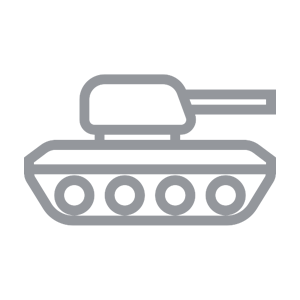
Militare
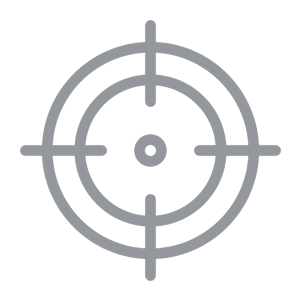
Sistemi di precisione
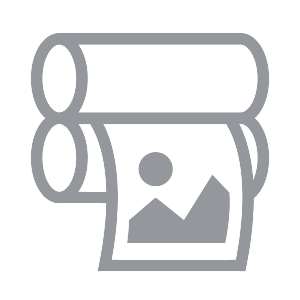
Rulli per verniciatura o stampa
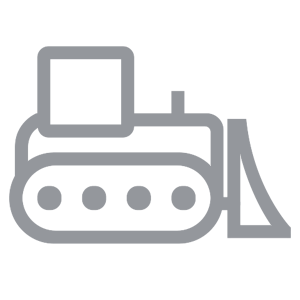
Movimento terra
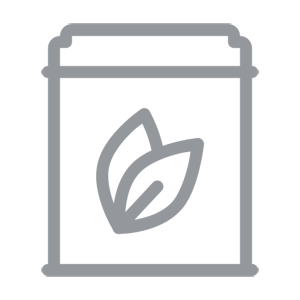