Decorative treatments
Anodic Oxidation
Decorative treatments
Anodic oxidation
Decorative treatments: anodic oxidation
Anodic oxidation is one of the most widely used treatments for covering metal objects and components. The purpose of this electrochemical treatment is to coat metals and improve their surface to make them more resistant to wear and corrosion.
In this article we are going to answer the most frequently asked questions such as “What is Anodizing?”, “How to Anodize a Metal?”, and we will see what are the advantages of anodizing and what are the differences with various types of oxidation.
How does anodizing take place?
Anodizing is a controlled process of metal oxidation that takes place by immersing the object in an electrolyte solution.
This creates a patina, a layer, which can be of different colors to improve aesthetics as well, and protects the object. Typically, anodizing is done on aluminum, but it is also applicable on other types of metal such as zinc, titanium, etc.
Anodizing can be divided into three main stages namely the preparation of the object to be treated, the actual anodizing, and the sealing of the anodized layer.
The process takes several hours, and it all depends on the size of the object to be treated.
What is the difference between aluminum and anodized aluminum?
Aluminum is an excellent material but being lightweight it is easily subject to corrosion, so anodizing treatment certainly makes it more durable.
The first difference present between aluminum and anodized aluminum is the type of surface, which for raw aluminum is uneven while for anodized aluminum is very smooth, hard, and uniform. This diversity is precisely the result of anodizing, which occurs by bathing the aluminum in chromic or sulfuric acid.
The other difference is that anodized aluminum can be of different colors to best suit one’s aesthetic taste.
Difference between anodizing and oxidation
The difference between anodizing and oxidation is based on the chemical process that takes place to obtain them. Aluminum and all its alloys undergo the natural process of oxidation simply by being in contact with air: the metal reacts to oxygen and an oxide layer is formed. Being a natural, uncontrolled process, however, it can go on to corrode the metal.
In contrast, anodizing is a controlled process where the oxide layer is artificially created on the surface of the metal and goes to protect it.
Hard anodic oxidation
Hard anodizing, unlike natural oxidation mentioned earlier, treats metal surfaces by means of electric current to develop an outer oxide layer that should increase hardness and corrosion resistance. In this way, the advantage you have is to create surfaces with high resistance to weathering, chemicals, and release high mechanical performance to the metal. It is precisely for the latter reason that it is widely used in industrial-type sectors such as automotive, aeronautics, etc.
Titanium anodic oxidation
We are looking at a very innovative process created to make titanium almost indestructible by improving its mechanical properties due to the layer that makes it insensitive to external stresses, and aesthetic by making it uniform and very shiny. Because of its performance, anodized titanium is used in aerospace, medical machinery, and automotive.
Chromic anodic oxidation
Chromic oxidation, unlike the others, is used more for achieving an aesthetically pleasing result as well as for creating the classic protective surface. By bathing the metal in chromic acid, it is possible to create interesting decorative parts especially for the automotive industry, such as wheels, door handles, and bumpers, in a wide variety of colors to make the design much more attractive and customizable.
How does the process take place?
The oxide that is formed is not due to material input but to a transformation of the original surface of the object. The aluminum surface undergoing anodizing is progressively oxidized from the outside of the surface progressing inward. The ‘oxide that is formed has a larger volume than the original metal (aluminum) so that apparently, from a dimensional point of view, there appears to be a contribution of material, in reality the thickness of oxide partly “penetrates” into the metal partly “grows” outward. In practice for a thickness of e.g. 10 microns, 5 microns penetrated and 5 microns expanded so the geometric increase amounts to 5 microns. Note that, on a diameter, the 10-micron thickness produces an increase in diameter of 10 microns, not 20.
Oxide also tends to form fairly uniformly in recesses, undercuts, and inside pipes. The structure of the oxide is very similar to the “honeycomb” structure with vertical tubules with respect to the thickness formed. These tubules are much less than a micron in diameter, but particular dyes can penetrate them, being able to impart a wide variety of colorations to the oxide layer. Following the formation of the oxide layer and, eventual staining, a pore-closing operation is performed in order to ensure compactness and corrosion resistance. This operation is called fixing and can be done cold or hot. In any case, the pores are closed. However, it turns out to be safer to heat fix especially for colored oxide layers.
Decorative treatments: anodic oxidation
Anodic oxidation is one of the most widely used treatments for covering metal objects and components. The purpose of this electrochemical treatment is to coat metals and improve their surface to make them more resistant to wear and corrosion.
In this article we are going to answer the most frequently asked questions such as “What is Anodizing?”, “How to Anodize a Metal?”, and we will see what are the advantages of anodizing and what are the differences with various types of oxidation.
How does anodizing take place?
Anodizing is a controlled process of metal oxidation that takes place by immersing the object in an electrolyte solution.
This creates a patina, a layer, which can be of different colors to improve aesthetics as well, and protects the object. Typically, anodizing is done on aluminum, but it is also applicable on other types of metal such as zinc, titanium, etc.
Anodizing can be divided into three main stages namely the preparation of the object to be treated, the actual anodizing, and the sealing of the anodized layer.
The process takes several hours, and it all depends on the size of the object to be treated.
What is the difference between aluminum and anodized aluminum?
Aluminum is an excellent material but being lightweight it is easily subject to corrosion, so the anodizing treatment certainly makes it more durable.
The first difference present between aluminum and anodized aluminum is the type of surface, which for raw aluminum is uneven while for anodized aluminum is very smooth, hard, and uniform. This diversity is precisely the result of anodizing, which occurs by bathing the aluminum in chromic or sulfuric acid.
The other difference is that anodized aluminum can be of different colors to best suit one’s aesthetic taste.
Difference between anodizing and oxidation
The difference between anodizing and oxidation is based on the chemical process that takes place to obtain them. Aluminum and all its alloys undergo the natural process of oxidation simply by being in contact with air: the metal reacts to oxygen and an oxide layer is formed. Being a natural, uncontrolled process, however, it can go on to corrode the metal.
In contrast, anodizing is a controlled process where the oxide layer is artificially created on the surface of the metal and goes to protect it.
Hard anodic oxidation
Hard anodizing, unlike natural oxidation mentioned earlier, treats metal surfaces by means of electric current to develop an outer oxide layer that should increase hardness and corrosion resistance. In this way, the advantage you have is to create surfaces with high resistance to weathering, chemicals, and release high mechanical performance to the metal. It is precisely for the latter reason that it is widely used in industrial-type sectors such as automotive, aeronautics, etc.
Titanium anodic oxidation
We are looking at a very innovative process created to make titanium almost indestructible by improving its mechanical properties due to the layer that makes it insensitive to external stresses, and aesthetic by making it uniform and very shiny. Because of its performance, anodized titanium is used in aerospace, medical machinery, and automotive.
Chromic anodic oxidation
Chromic oxidation, unlike the others, is used more for achieving an aesthetically pleasing result as well as for creating the classic protective surface. By bathing the metal in chromic acid, it is possible to create interesting decorative parts especially for the automotive industry, such as wheels, door handles, and bumpers, in a wide variety of colors to make the design much more attractive and customizable.
Treatable materials
- Aluminum and its alloys, from extrusion, rolling, 2011, 11S, 6060, 6082, 7075, Ergal, Anticorodal;
- Low-pressure die-casting aluminum in shell.
Regulations
- UNI-EN 12373-1 – UNI 4522
Possible finishes
- White (neutral)
- Black
- Blue
- Red
Maximum treatable size
500 x 250 x 800 mm
Treatable materials
- Aluminum and its alloys, from extrusion, rolling, 2011, 11S, 6060, 6082, 7075, Ergal, Anticorodal;
- Low-pressure die-casting aluminum in shell.
Possible finishes
- White (neutral)
- Black
- Blue
- Red
Regulations
- UNI-EN 12373-1 – UNI 4522
Maximum treatable size
500 x 250 x 800 mm
Sectors
implementing
implementing
Application areas
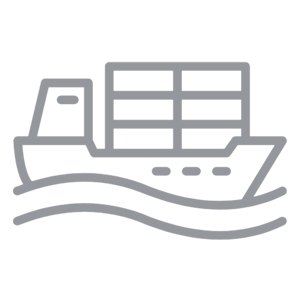
Naval
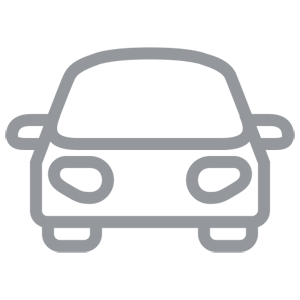
Automotive
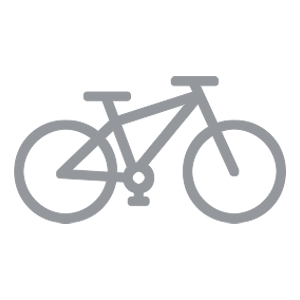
Cycle
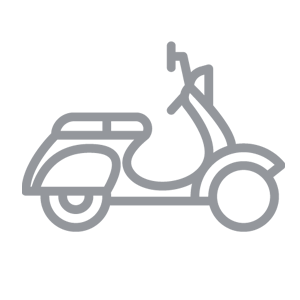
Motorcycle
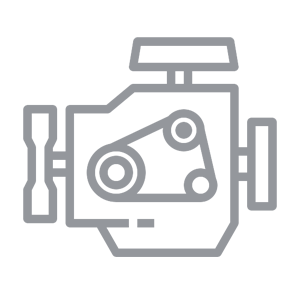
Mechanic
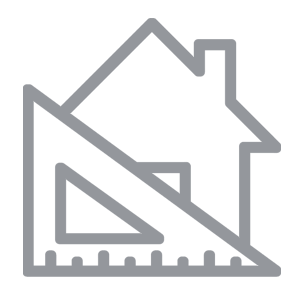
Architectural
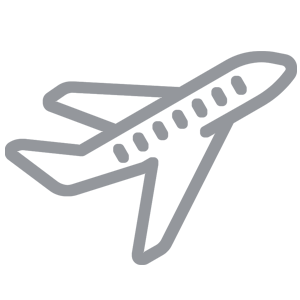
Aeronautical
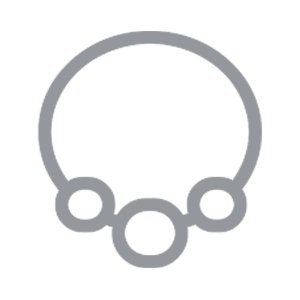