Trattamenti decorativi
Ossidazione Anodica
Trattamenti decorativi
Ossidazione anodica
Trattamenti decorativi: l'ossidazione anodica
L’ ossidazione anodica è uno dei trattamenti più utilizzati per la copertura di oggetti e componenti metallici. Lo scopo di questo trattamento elettrochimico è rivestire i metalli e migliorarne la superficie per renderli più resistenti all’usura e alla corrosione.
In questo articolo andremo a rispondere alle domande più ricorrenti come “Che cosa vuol dire anodizzazione?”, “Come Anodizzare un metallo?”, e vedremo quali sono i vantaggi dell’anodizzazione e quali sono le differenze con i vari tipi di ossidazione.
Come avviene la anodizzazione?
L’anodizzazione è un processo di ossidazione del metallo che avviene in maniera controllata e si svolge immergendo l’oggetto in una soluzione elettrolitica.
In questo modo si crea una patina, uno strato, che può essere di diversi colori per migliorare anche l’estetica, e protegge l’oggetto. In genere l’anodizzazione viene effettuata sull’alluminio, ma è applicabile anche su altri tipo di metallo come lo zinco, il titanio ecc.
L’anodizzazione si può dividere in tre fasi principali ovvero la preparazione dell’oggetto da trattare, l’anodizzazione vera e propria, e il sigillo dello strato anodizzato.
Il processo dura diverse ore e tutto dipende dalle dimensioni dell’oggetto da trattare.
Che differenza c’è tra alluminio e alluminio anodizzato?
L’alluminio è un ottimo materiale ma essendo leggero è soggetto facilmente a corrosione, quindi il trattamento anodizzante lo rende certamente più resistente.
La prima differenza presente tra alluminio e alluminio anodizzato è la tipologia di superficie che per l’alluminio grezzo non è uniforme mentre per l’anodizzato è molto liscia, dura e uniforme. Questa diversità è proprio frutto dell’anodizzazione che avviene facendo un bagno dell’alluminio nell’acido cromico o in quello solforico.
L’altra differenza è che all’alluminio anodizzato può essere di diversi colori per soddisfare il proprio gusto estetico al meglio.
Differenza tra anodizzazione e ossidazione
La differenza tra anodizzazione e ossidazione si basa sul processo chimico che avviene per ottenerle. L’alluminio e tutte le sue leghe subiscono il processo naturale di ossidazione semplicemente stando a contatto con l’aria: il metallo reagisce all’ossigeno e si forma uno strato di ossido. Essendo un processo naturale, non controllato, può però andare a corrodere il metallo.
L’anodizzazione è invece un processo controllato dove lo strato di ossido viene creato in maniera artificiale sulla superficie del metallo e va a proteggerlo.
Ossidazione anodica dura
L’ossidazione anodica dura, a differenza dell’ossidazione naturale prima citata, tratta le superfici metalliche tramite corrente elettrica per sviluppare uno strato esterno di ossido che deve aumentare la durezza e la resistenza alla corrosione. In questo modo il vantaggio che si ha è quello di creare superfici ad alta resistenza agli agenti atmosferici, chimici e rilasciare al metallo alte prestazioni meccaniche. Proprio per quest’ultima ragione viene molto utilizzata nei settori di tipo industriale come l’automotive, l’aeronautica ecc.
Ossidazione anodica titanio
Ci troviamo davanti ad un processo molto innovativo creato per rendere quasi indistruttibile il titanio migliorandone le sue caratteristiche meccaniche grazie allo strato che lo rende poco sensibile alle sollecitazioni esterne, ed estetiche rendendolo uniforme e molto brillante. Grazie alle sue prestazioni il titanio anodizzato viene utilizzato nel settore aerospaziale, in campo medico per i macchinari e nell’automotive.
Ossidazione anodica cromica
L’ossidazione cromica, a differenza delle altre, viene utilizzata maggiormente per ottenere un risultato estetico gradevole oltre che per la creazione della classica superficie protettiva. Grazie al bagno del metallo nell’acido cromico è possibile creare parti decorative interessanti soprattutto per il settore automobilistico come ad esempio i cerchi, le maniglie, i paraurti, dai più svariati colori per rendere il design molto più accattivante e personalizzabile.
Come avviene il processo?
L’ossido che si forma non è dovuto ad un apporto di materiale ma ad una trasformazione della superficie originale dell’oggetto. La superficie di alluminio sottoposta ad anodizzazione viene ossidata progressivamente dall’esterno della superficie progredendo verso l’interno. L’ ossido che si forma ha un volume maggiore del metallo (alluminio) originario per cui apparentemente, dal punto di vista dimensionale, sembra vi sia un apporto di materiale, in realtà lo spessore di ossido in parte “penetra” nel metallo in parte “cresce” verso l’esterno. In pratica per uno spessore di es. 10 micron, 5 micron sono penetrati e 5 micron si sono espansi per cui l’aumento geometrico ammonta a 5 micron. Da notare che, su un diametro, lo spessore di 10 micron produce un aumento del diametro pari a 10 micron e non 20.
L’ossido tende a formarsi abbastanza uniformemente anche nei recessi, nei sottosquadra, all’interno di tubi. La struttura dell’ossido è molto simile alla struttura del “nido d’ape” con tubuli verticali rispetto allo spessore formato. Questi tubuli hanno un diametro molto inferiore al micron, ma particolari coloranti vi possono penetrare, potendo conferire allo strato di ossido una grande varietà di colorazioni. Successivamente alla formazione dello strato di ossido e, alla eventuale colorazione, viene eseguita una operazione di chiusura dei pori al fine di garantire compattezza e resistenza alla corrosione. Questa operazione prende il nome di fissaggio e può avvenire a freddo o a caldo. In ogni caso i pori vengono chiusi. Risulta tuttavia più sicura l’operazione di fissaggio a caldo soprattutto per gli strati di ossido colorato.
Trattamenti decorativi: l'ossidazione anodica
L’ ossidazione anodica è uno dei trattamenti più utilizzati per la copertura di oggetti e componenti metallici. Lo scopo di questo trattamento elettrochimico è rivestire i metalli e migliorarne la superficie per renderli più resistenti all’usura e alla corrosione.
In questo articolo andremo a rispondere alle domande più ricorrenti come “Che cosa vuol dire anodizzazione?”, “Come Anodizzare un metallo?”, e vedremo quali sono i vantaggi dell’anodizzazione e quali sono le differenze con i vari tipi di ossidazione.
Come avviene la anodizzazione?
L’anodizzazione è un processo di ossidazione del metallo che avviene in maniera controllata e si svolge immergendo l’oggetto in una soluzione elettrolitica.
In questo modo si crea una patina, uno strato, che può essere di diversi colori per migliorare anche l’estetica, e protegge l’oggetto. In genere l’anodizzazione viene effettuata sull’alluminio, ma è applicabile anche su altri tipo di metallo come lo zinco, il titanio ecc.
L’anodizzazione si può dividere in tre fasi principali ovvero la preparazione dell’oggetto da trattare, l’anodizzazione vera e propria, e il sigillo dello strato anodizzato.
Il processo dura diverse ore e tutto dipende dalle dimensioni dell’oggetto da trattare.
Che differenza c’è tra alluminio e alluminio anodizzato?
L’alluminio è un ottimo materiale ma essendo leggero è soggetto facilmente a corrosione, quindi il trattamento anodizzante lo rende certamente più resistente.
La prima differenza presente tra alluminio e alluminio anodizzato è la tipologia di superficie che per l’alluminio grezzo non è uniforme mentre per l’anodizzato è molto liscia, dura e uniforme. Questa diversità è proprio frutto dell’anodizzazione che avviene facendo un bagno dell’alluminio nell’acido cromico o in quello solforico.
L’altra differenza è che all’alluminio anodizzato può essere di diversi colori per soddisfare il proprio gusto estetico al meglio.
Differenza tra anodizzazione e ossidazione
La differenza tra anodizzazione e ossidazione si basa sul processo chimico che avviene per ottenerle. L’alluminio e tutte le sue leghe subiscono il processo naturale di ossidazione semplicemente stando a contatto con l’aria: il metallo reagisce all’ossigeno e si forma uno strato di ossido. Essendo un processo naturale, non controllato, può però andare a corrodere il metallo.
L’anodizzazione è invece un processo controllato dove lo strato di ossido viene creato in maniera artificiale sulla superficie del metallo e va a proteggerlo.
Ossidazione anodica dura
L’ossidazione anodica dura, a differenza dell’ossidazione naturale prima citata, tratta le superfici metalliche tramite corrente elettrica per sviluppare uno strato esterno di ossido che deve aumentare la durezza e la resistenza alla corrosione. In questo modo il vantaggio che si ha è quello di creare superfici ad alta resistenza agli agenti atmosferici, chimici e rilasciare al metallo alte prestazioni meccaniche. Proprio per quest’ultima ragione viene molto utilizzata nei settori di tipo industriale come l’automotive, l’aeronautica ecc.
Ossidazione anodica titanio
Ci troviamo davanti ad un processo molto innovativo creato per rendere quasi indistruttibile il titanio migliorandone le sue caratteristiche meccaniche grazie allo strato che lo rende poco sensibile alle sollecitazioni esterne, ed estetiche rendendolo uniforme e molto brillante. Grazie alle sue prestazioni il titanio anodizzato viene utilizzato nel settore aerospaziale, in campo medico per i macchinari e nell’automotive.
Ossidazione anodica cromica
L’ossidazione cromica, a differenza delle altre, viene utilizzata maggiormente per ottenere un risultato estetico gradevole oltre che per la creazione della classica superficie protettiva. Grazie al bagno del metallo nell’acido cromico è possibile creare parti decorative interessanti soprattutto per il settore automobilistico come ad esempio i cerchi, le maniglie, i paraurti, dai più svariati colori per rendere il design molto più accattivante e personalizzabile.
Materiali trattabili
- Alluminio e sue leghe, da estrusione, laminazione, 2011, 11S, 6060, 6082, 7075, Ergal, Anticorodal;
- Alluminio da fusione in bassa pressione, in conchiglia.
Normative
- UNI-EN 12373-1 – UNI 4522
Possibili finiture
- Bianca (neutra)
- Nera
- Blu
- Rossa
Dimensioni massime trattabili
500 x 250 x 800 mm
Materiali trattabili
- Alluminio e sue leghe, da estrusione, laminazione, 2011, 11S, 6060, 6082, 7075, Ergal, Anticorodal;
- Alluminio da fusione in bassa pressione, in conchiglia.
Possibili finiture
- Bianca (neutra)
- Nera
- Blu
- Rossa
Normative
- UNI-EN 12373-1 – UNI 4522
Dimensioni massime trattabili
500 x 250 x 800 mm
Settori
d'applicazione
d'applicazione
Settori d'applicazione
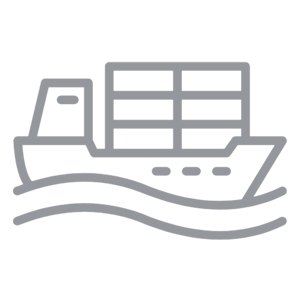
Navale
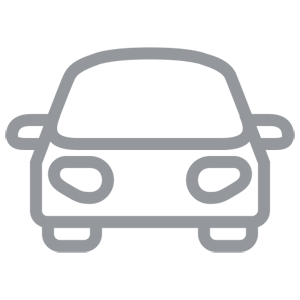
Automotive
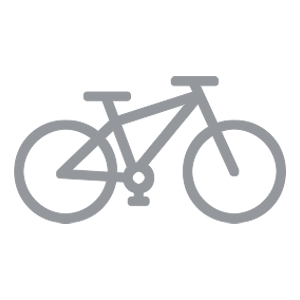
Ciclo
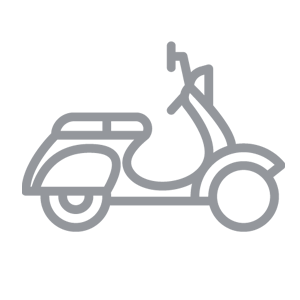
Motociclo
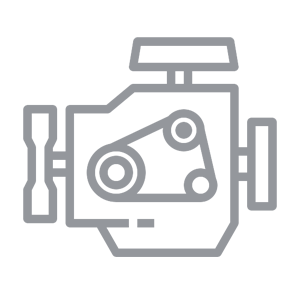
Meccanico
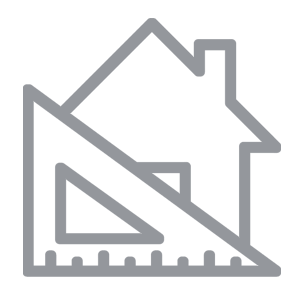
Architettonico
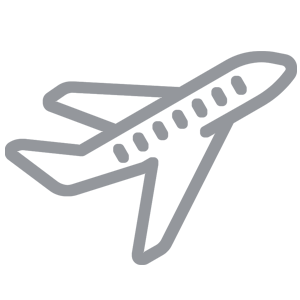
Aeronautico
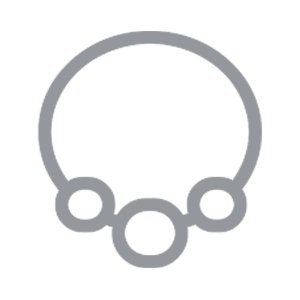