Protective treatments
Electrolytic galvanizing
Protective treatments
Electrolytic galvanizing
Protective treatments: electrolytic galvanizing
What is electrolytic galvanizing?
Electrolytic galvanizing is a process of depositing zinc on metal objects through the application of electric current. This takes place in a galvanic cell, where zinc is reduced at the negative pole (cathode), and the amount of zinc deposited is proportional to the through current. The process takes place at temperatures of 20-25°C, and is known as “cold galvanizing” to distinguish it from hot dip galvanizing, which operates at temperatures around 450°C.
Galvanizing is widely used on ferrous materials to take advantage of the cathodic/sacrificial protection effect of zinc. In corrosive environments, zinc corrodes first, acting as a sacrificial layer and preventing corrosion of the underlying iron.
The process involves current flowing through the electrolytic cell, migrating zinc ions to the material to be galvanized along the flow lines of the electrolytic field. This results in varying deposition thickness, with areas of shorter path and peaks showing higher thicknesses.
To preserve the aesthetic appearance and improve the corrosion durability of electrodeposited zinc, treatments such as passivation and sealing are performed. Passivation creates a stable layer of zinc salts that contains other elements such as chromium, cobalt, and silicon, providing stability against corrosive agents. Sealing, on the other hand, consists of an organic film that chemically bonds to the passivation, adding additional protection.
During the galvanizing process, an undesirable reaction of hydrogen formation occurs. To prevent stress due to hydrogen absorption by the ferrous material, especially in materials with high tensile strength, it is necessary to carry out “dehydrogenation” immediately after galvanizing. This step prevents breakage of components in operation and before use.
How does the process take place?
The oxide that is formed is not due to material input but to a transformation of the original surface of the object. The aluminum surface undergoing anodizing is progressively oxidized from the outside of the surface progressing inward. The ‘oxide that is formed has a larger volume than the original metal (aluminum) so that apparently, from a dimensional point of view, it seems away is a material contribution, in reality the thickness of oxide partly “penetrates” into the metal partly “grows” outward. In practice for a thickness of e.g. 10 microns, 5 microns penetrated and 5 microns expanded so the geometric increase amounts to 5 microns. Note that, on a diameter, the 10-micron thickness produces an increase in diameter of 10 microns, not 20.
Oxide also tends to form fairly uniformly in recesses, undercuts, and inside pipes. The structure of the oxide is very similar to the “honeycomb” structure with vertical tubules with respect to the thickness formed. These tubules are much less than a micron in diameter, but particular dyes can penetrate them, being able to impart a wide variety of colorations to the oxide layer. Following the formation of the oxide layer and, eventual staining, a pore-closing operation is performed in order to ensure compactness and corrosion resistance. This operation is called fixing and can be done cold or hot. in any case the pores are closed, however, it turns out to be safer to heat fix especially for colored oxide layers.
Protective treatments: electrolytic galvanizing
What is electrolytic galvanizing?
Electrolytic galvanizing is a process of depositing zinc on metal objects through the application of electric current. This takes place in a galvanic cell, where zinc is reduced at the negative pole (cathode), and the amount of zinc deposited is proportional to the through current. The process takes place at temperatures of 20-25°C, and is known as “cold galvanizing” to distinguish it from hot dip galvanizing, which operates at temperatures around 450°C.
Galvanizing is widely used on ferrous materials to take advantage of the cathodic/sacrificial protection effect of zinc. In corrosive environments, zinc corrodes first, acting as a sacrificial layer and preventing corrosion of the underlying iron.
The process involves current flowing through the electrolytic cell, migrating zinc ions to the material to be galvanized along the flow lines of the electrolytic field. This results in varying deposition thickness, with areas of shorter path and peaks showing higher thicknesses.
To preserve the aesthetic appearance and improve the corrosion durability of electrodeposited zinc, treatments such as passivation and sealing are performed. Passivation creates a stable layer of zinc salts that contains other elements such as chromium, cobalt, and silicon, providing stability against corrosive agents. Sealing, on the other hand, consists of an organic film that chemically bonds to the passivation, adding additional protection.
During the galvanizing process, an undesirable reaction of hydrogen formation occurs. To prevent stress due to hydrogen absorption by the ferrous material, especially in materials with high tensile strength, it is necessary to carry out “dehydrogenation” immediately after galvanizing. This step prevents breakage of components in operation and before use.
How does the process take place?
The oxide that is formed is not due to material input but to a transformation of the original surface of the object. The aluminum surface undergoing anodizing is progressively oxidized from the outside of the surface progressing inward. The ‘oxide that is formed has a larger volume than the original metal (aluminum) so that apparently, from a dimensional point of view, it seems away is a material contribution, in reality the thickness of oxide partly “penetrates” into the metal partly “grows” outward. In practice for a thickness of e.g. 10 microns, 5 microns penetrated and 5 microns expanded so the geometric increase amounts to 5 microns. Note that, on a diameter, the 10-micron thickness produces an increase in diameter of 10 microns, not 20.
Oxide also tends to form fairly uniformly in recesses, undercuts, and inside pipes. The structure of the oxide is very similar to the “honeycomb” structure with vertical tubules with respect to the thickness formed. These tubules are much less than a micron in diameter, but particular dyes can penetrate them, being able to impart a wide variety of colorations to the oxide layer. Following the formation of the oxide layer and, eventual staining, a pore-closing operation is performed in order to ensure compactness and corrosion resistance. This operation is called fixing and can be done cold or hot. in any case the pores are closed, however, it turns out to be safer to heat fix especially for colored oxide layers.
Treatable materials
- Carbon steel
- Iron
- AVP
- AVZ
- C40, C45
- 8.8, 10.9, 12.9
- Zama Solo in Rotobarile
Regulations
- UNI ISO 2081
- UNI ISO 4520
- ASTM B633
- Daimler Mercedes DBL 8451
- DIN 50979
- BMW GS900
- FIAT 9.57405
- Ducati ST-STR-008
- Volkswagen VW 13750 TL 217
- Volvo STD121-004
Possible finishes
- White passivation (chrome 3)
- High strength passivation (chrome 3)
- Black passivation (chrome 3)
Maximum treatable size
2,450 x 500 x 1,000 mm
Treatable materials
- Carbon steel
- Iron
- AVP
- AVZ
- C40, C45
- 8.8, 10.9, 12.9
- Zama Solo in Rotobarile
Possible finishes
- White passivation (chrome 3)
- High strength passivation (chrome 3)
- Black passivation (chrome 3)
Regulations
- UNI ISO 2081
- UNI ISO 4520
- ASTM B633
- Daimler Mercedes DBL 8451
- DIN 50979
- BMW GS900
- FIAT 9.57405
- Ducati ST-STR-008
- Volkswagen VW 13750 TL 217
- Volvo STD121-004
Maximum treatable size
2,450 x 500 x 1,000 mm
Sectors
implementing
implementing
Application areas
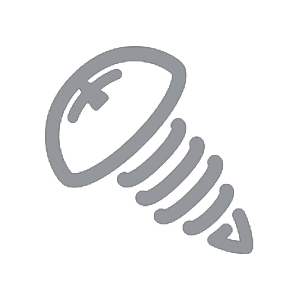
Hardware, nuts and bolts
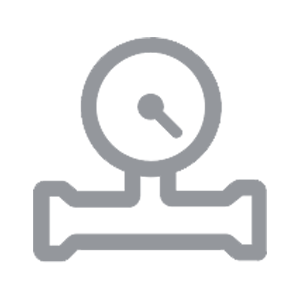
Fittings
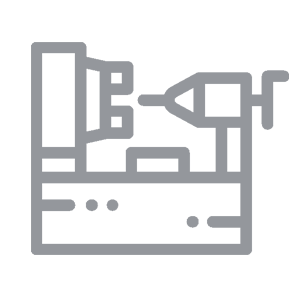
Sliced, sheet, plate, and turned
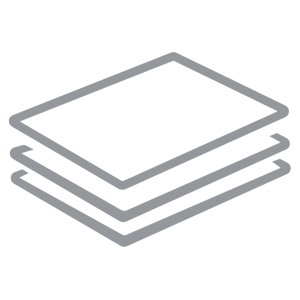