Trattamenti protettivi
Zincatura elettrolitica
Trattamenti protettivi
Zincatura elettrolitica
Trattamenti protettivi: la zincatura elettrolitica
Cos’è la zincatura elettrolitica?
La zincatura elettrolitica è un processo di deposizione di zinco su oggetti metallici attraverso l’applicazione di corrente elettrica. Questo avviene in una cella galvanica, dove lo zinco viene ridotto al polo negativo (catodo), e la quantità di zinco depositato è proporzionale alla corrente passante. Il processo avviene a temperature di 20-25°C, ed è noto come “zincatura a freddo” per distinguerlo dalla zincatura a caldo che opera a temperature intorno ai 450°C.
La zincatura è ampiamente utilizzata su materiali ferrosi per sfruttare l’effetto di protezione catodica/sacrificale dello zinco. In ambienti corrosivi, lo zinco si corrode per primo, agendo come uno strato sacrificale e impedendo la corrosione del ferro sottostante.
Il processo prevede che la corrente attraversi la cella elettrolitica, migrando gli ioni di zinco verso il materiale da zincare lungo le linee di flusso del campo elettrolitico. Ciò determina uno spessore di deposito variabile, con zone di percorso più breve e punte che mostrano spessori più elevati.
Per preservare l’aspetto estetico e migliorare la durata alla corrosione dello zinco elettrodepositato, vengono eseguiti trattamenti come la passivazione e la sigillatura. La passivazione crea uno strato stabile di sali di zinco che contiene altri elementi come cromo, cobalto e silicio, fornendo stabilità contro gli agenti corrosivi. La sigillatura, invece, consiste in un film organico che si lega chimicamente alla passivazione, aggiungendo ulteriore protezione.
Durante il processo di zincatura, si verifica una reazione indesiderata di formazione di idrogeno. Per prevenire la tensione dovuta all’assorbimento di idrogeno da parte del materiale ferroso, soprattutto in materiali con elevato carico di rottura, è necessario eseguire la “deidrogenazione” immediatamente dopo la zincatura. Questo passo evita rotture dei componenti in fase operativa e prima dell’utilizzo.
Come avviene il processo?
L’ossido che si forma non è dovuto ad un apporto di materiale ma ad una trasformazione della superficie originale dell’oggetto. La superficie di alluminio sottoposta ad anodizzazione viene ossidata progressivamente dall’esterno della superficie progredendo verso l’interno. L’ ossido che si forma ha un volume maggiore del metallo (alluminio) originario per cui apparentemente, dal punto di vista dimensionale, sembra via sia un apporto di materiale, in realtà lo spessore di ossido in parte “penetra” nel metallo in parte “cresce” verso l’esterno. In pratica per uno spessore di es. 10 micron, 5 micron sono penetrati e 5 micron si sono espansi per cui l’aumento geometrico ammonta a 5 micron. Da notare che, su un diametro, lo spessore di 10 micron produce un aumento del diametro pari a 10 micron e non 20.
L’ossido tende a formarsi abbastanza uniformemente anche nei recessi, nei sottosquadra, all’interno di tubi. La struttura dell’ossido è molto simile alla struttura del “nido d’ape” con tubuli verticali rispetto allo spessore formato. Questi tubuli hanno un diametro molto inferiore al micron, ma particolari coloranti vi possono penetrare, potendo conferire allo strato di ossido una grande varietà di colorazioni. Successivamente alla formazione dello strato di ossido e, alla eventuale colorazione, viene eseguita una operazione di chiusura dei pori al fine di garantire compattezza e resistenza alla corrosione. Questa operazione prende il nome di fissaggio e può avvenire a freddo o a caldo. in ogni caso i pori vengono chiusi, risulta tuttavia più sicura l’operazione di fissaggio a caldo soprattutto per gli strati di ossido colorato.
Trattamenti protettivi: la zincatura elettrolitica
Cos’è la zincatura elettrolitica?
La zincatura elettrolitica è un processo di deposizione di zinco su oggetti metallici attraverso l’applicazione di corrente elettrica. Questo avviene in una cella galvanica, dove lo zinco viene ridotto al polo negativo (catodo), e la quantità di zinco depositato è proporzionale alla corrente passante. Il processo avviene a temperature di 20-25°C, ed è noto come “zincatura a freddo” per distinguerlo dalla zincatura a caldo che opera a temperature intorno ai 450°C.
La zincatura è ampiamente utilizzata su materiali ferrosi per sfruttare l’effetto di protezione catodica/sacrificale dello zinco. In ambienti corrosivi, lo zinco si corrode per primo, agendo come uno strato sacrificale e impedendo la corrosione del ferro sottostante.
Il processo prevede che la corrente attraversi la cella elettrolitica, migrando gli ioni di zinco verso il materiale da zincare lungo le linee di flusso del campo elettrolitico. Ciò determina uno spessore di deposito variabile, con zone di percorso più breve e punte che mostrano spessori più elevati.
Per preservare l’aspetto estetico e migliorare la durata alla corrosione dello zinco elettrodepositato, vengono eseguiti trattamenti come la passivazione e la sigillatura. La passivazione crea uno strato stabile di sali di zinco che contiene altri elementi come cromo, cobalto e silicio, fornendo stabilità contro gli agenti corrosivi. La sigillatura, invece, consiste in un film organico che si lega chimicamente alla passivazione, aggiungendo ulteriore protezione.
Durante il processo di zincatura, si verifica una reazione indesiderata di formazione di idrogeno. Per prevenire la tensione dovuta all’assorbimento di idrogeno da parte del materiale ferroso, soprattutto in materiali con elevato carico di rottura, è necessario eseguire la “deidrogenazione” immediatamente dopo la zincatura. Questo passo evita rotture dei componenti in fase operativa e prima dell’utilizzo.
Come avviene il processo?
L’ossido che si forma non è dovuto ad un apporto di materiale ma ad una trasformazione della superficie originale dell’oggetto. La superficie di alluminio sottoposta ad anodizzazione viene ossidata progressivamente dall’esterno della superficie progredendo verso l’interno. L’ ossido che si forma ha un volume maggiore del metallo (alluminio) originario per cui apparentemente, dal punto di vista dimensionale, sembra via sia un apporto di materiale, in realtà lo spessore di ossido in parte “penetra” nel metallo in parte “cresce” verso l’esterno. In pratica per uno spessore di es. 10 micron, 5 micron sono penetrati e 5 micron si sono espansi per cui l’aumento geometrico ammonta a 5 micron. Da notare che, su un diametro, lo spessore di 10 micron produce un aumento del diametro pari a 10 micron e non 20.
L’ossido tende a formarsi abbastanza uniformemente anche nei recessi, nei sottosquadra, all’interno di tubi. La struttura dell’ossido è molto simile alla struttura del “nido d’ape” con tubuli verticali rispetto allo spessore formato. Questi tubuli hanno un diametro molto inferiore al micron, ma particolari coloranti vi possono penetrare, potendo conferire allo strato di ossido una grande varietà di colorazioni. Successivamente alla formazione dello strato di ossido e, alla eventuale colorazione, viene eseguita una operazione di chiusura dei pori al fine di garantire compattezza e resistenza alla corrosione. Questa operazione prende il nome di fissaggio e può avvenire a freddo o a caldo. in ogni caso i pori vengono chiusi, risulta tuttavia più sicura l’operazione di fissaggio a caldo soprattutto per gli strati di ossido colorato.
Materiali trattabili
- Acciaio al carbonio
- Ferro
- AVP
- AVZ
- C40, C45
- 8.8, 10.9, 12.9
- Zama Solo a Rotobarile
Normative
- UNI ISO 2081
- UNI ISO 4520
- ASTM B633
- Daimler Mercedes DBL 8451
- DIN 50979
- BMW GS900
- FIAT 9.57405
- Ducati ST-STR-008
- Volkswagen VW 13750 TL 217
- Volvo STD121-004
Possibili finiture
- Passivazione bianca (cromo 3)
- Passivazione alta resistenza (cromo 3)
- Passivazione nera (cromo 3)
Dimensioni massime trattabili
2.450 x 500 x 1.000 mm
Materiali trattabili
- Acciaio al carbonio
- Ferro
- AVP
- AVZ
- C40, C45
- 8.8, 10.9, 12.9
- Zama Solo a Rotobarile
Possibili finiture
- Passivazione bianca (cromo 3)
- Passivazione alta resistenza (cromo 3)
- Passivazione nera (cromo 3)
Normative
- UNI ISO 2081
- UNI ISO 4520
- ASTM B633
- Daimler Mercedes DBL 8451
- DIN 50979
- BMW GS900
- FIAT 9.57405
- Ducati ST-STR-008
- Volkswagen VW 13750 TL 217
- Volvo STD121-004
Dimensioni massime trattabili
2.450 x 500 x 1.000 mm
Settori
d'applicazione
d'applicazione
Settori d'applicazione
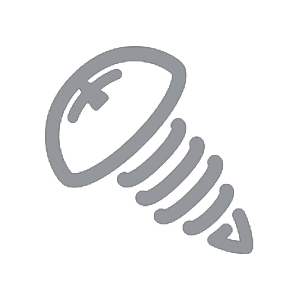
Viteria, dadi e bulloni
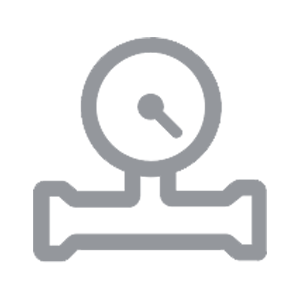
Raccorderia
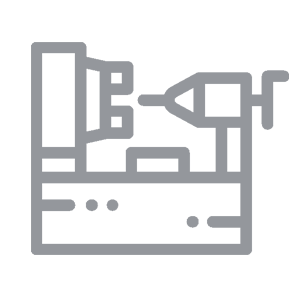
Tranciati, lamiere, lastre e torniti
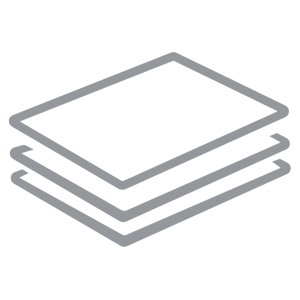