Decorative treatments
Chrome plating
Decorative treatments
CHROME
Decorative treatments: chrome plating
Metal chrome plating represents a coating process that gives a bright and durable appearance to various metal materials. This technique, which originated in the 19th century, has found wide use in the manufacturing industry to improve the aesthetics and durability of objects and components. Decorative chrome plating, in particular, is notable for its use in the design and furniture industry, where it is used to lend elegance and prestige to a wide range of products, from furniture to home accessories. This type of chrome plating not only adds aesthetic value, but also offers protection against oxidation and wear, ensuring a durable and easy-to-clean surface. In this introduction, we will explore the process of metal chrome plating in more depth, focusing in particular on its decorative application and its implications in design and industry.
Chrome plating can be applied to a wide range of metals, including:
- Aluminum: Chrome plating on aluminum provides a shiny, corrosion-resistant appearance, making it ideal for a variety of industrial and decorative applications.
- Stainless steel: Despite its corrosion resistance, stainless steel can be chromed to further improve its aesthetic appearance and protection against oxidation.
- Brass: Chrome plating on brass adds a smooth, polished finish, lending an elegant appearance to a wide range of products from furniture to accessories.
- Copper: Copper can be chromed to add corrosion resistance and improve aesthetic appearance, particularly useful in decorative applications.
- Iron: Chrome plating of iron provides a durable and shiny finish, making it suitable for a variety of industrial and decorative applications.
- Zinc alloys: Zinc alloys, such as zamak, can be chromed to improve their appearance and protect them from corrosion.
Chrome plating can be applied to many other types of metals as long as they are properly prepared for the coating process. However, the choice of metal will depend on the specific needs of the application and the desired properties of the finished product.
What are its characteristics?
Decorative chrome plating, glossy, matte or black, has these peculiarities:
- esthetically much appreciated;
- Excellent corrosion resistance;
- excellent abrasion resistance.
How does the Chrome Plating Process work?
Chrome plating is a meticulous process that transforms the surface of a metal, giving it a shiny, corrosion-resistant finish. It begins with thorough preparation of the surface, which is cleaned to remove any traces of dirt, grease, or corrosion that could compromise the final result. Then, in some cases, a layer of nickel is applied to improve adhesion of the chromium coating and corrosion resistance.
Chromium coating is applied through an electrolytic or spray process. In electroplating, the part to be chromed is immersed in a solution containing chromium, acting as the cathode, while a chromium anode is present in the same solution. When an electric current is applied, chromium ions are reduced and deposited on the surface of the metal piece. In spray chromium plating, on the other hand, chromium particles are sprayed onto the surface of the metal part and then melted by heating to form the coating.
After the chrome coating is applied, the surface is finished by polishing or sanding to achieve the desired finish, removing any imperfections. Finally, the part undergoes quality control to ensure that it meets the required standards in terms of coating adhesion, thickness, and aesthetic appearance.
This process requires great precision and attention to detail to achieve optimal results, both aesthetically and functionally.
How many types of chrome plating are there?
There are several types of chrome plating, each of which offers specific advantages depending on the needs of the application. Some of the main types of chrome plating include:
- Decorative chrome plating: This type of chrome plating is mainly aimed at improving the aesthetic appearance of metal materials. It is used to give a shiny, glossy finish to items such as automotive parts, furniture, home accessories and jewelry.
- Industrial chrome plating: Industrial chrome plating is designed to provide corrosion and wear protection in industrial and commercial environments. This type of chrome plating is often used on mechanical parts, industrial equipment, tools and electronic components.
- Hard chrome plating: This form of chrome plating, also known as hard chrome plating, employs a thick chrome coating to improve resistance to wear, abrasion and corrosion. It is commonly used on drive shafts, hydraulic cylinders, cutting tools and other surfaces subject to high mechanical stress.
- Black chrome plating: This process involves applying a black chromium oxide coating to metal surfaces, providing a dark, matte finish. Black chrome plating is often used for decorative purposes or to improve the lubrication and corrosion resistance properties of metal parts.
- Trivalent chromium plating: This form of chromium plating uses trivalent chromium compounds instead of hexavalent chromium, thus reducing the environmental impact and health risk associated with traditional chromium plating. Trivalent chromium plating still offers excellent corrosion and abrasion resistance and is increasingly used as a more sustainable alternative to hexavalent chromium plating.
These are just some of the main types of chrome plating, but there are also other specialized variations depending on the specific needs of the application.
What is the difference between electroplating and hot chromium plating?
Electroplating and hot chromium plating are two different methods of applying a chromium coating to a metal surface, and they differ mainly in the process used and the properties of the resulting coating.
Galvanic chromium plating, also known as electroplating, is a process that involves immersing the metal part to be chromed in an electrolyte solution containing chromium. In this process, the metal piece serves as the cathode and a chromium anode is immersed in the solution. When an electric current is applied, chromium ions in the solution are reduced and deposited on the surface of the metal piece, forming the chromium coating. This method is commonly used to achieve thin, uniform coatings that are ideal for decorative and protective applications.
On the other hand, hot chromium plating is a process in which the chromium coating is applied by casting to the surface of the metal part. During this process, a chromium alloy is melted and applied to the surface of the metal to be chromed by dipping or by a spraying process. The resulting coating is usually thicker and stronger than galvanic chrome plating, making it suitable for applications where greater resistance to wear and corrosion is required, such as mechanical components subject to high stresses.
Thus, the main difference between electroplating and hot chromium plating lies in the process of applying the chromium coating: while electroplating is done by an electrolytic process, hot chromium plating involves melting and directly applying chromium to the metal surface.
Metal chrome plating and decorative chrome plating represent two fundamental processes for improving the aesthetic appearance, strength, and durability of metal materials. Metal chrome plating offers solid protection from corrosion and wear, making metal components suitable for a wide range of industrial and commercial applications. On the other hand, decorative chrome plating goes beyond mere functionality, lending distinctive elegance and style to objects and surfaces, ranging from home furnishings to design products. Both processes involve meticulous attention to detail and strict quality control to ensure optimal results. The choice between metal chrome plating and decorative chrome plating depends on the specific needs of the application and the desired aesthetic goal, but both help to enhance and improve the appearance of metal materials in the industrial and design landscape.
Decorative treatments: chrome plating
Metal chrome plating represents a coating process that gives a bright and durable appearance to various metal materials. This technique, which originated in the 19th century, has found wide use in the manufacturing industry to improve the aesthetics and durability of objects and components. Decorative chrome plating, in particular, is notable for its use in the design and furniture industry, where it is used to lend elegance and prestige to a wide range of products, from furniture to home accessories. This type of chrome plating not only adds aesthetic value, but also offers protection against oxidation and wear, ensuring a durable and easy-to-clean surface. In this introduction, we will explore the process of metal chrome plating in more depth, focusing in particular on its decorative application and its implications in design and industry.
Chrome plating can be applied to a wide range of metals, including:
- Aluminum: Chrome plating on aluminum provides a shiny, corrosion-resistant appearance, making it ideal for a variety of industrial and decorative applications.
- Stainless steel: Despite its corrosion resistance, stainless steel can be chromed to further improve its aesthetic appearance and protection against oxidation.
- Brass: Chrome plating on brass adds a smooth, polished finish, lending an elegant appearance to a wide range of products from furniture to accessories.
- Copper: Copper can be chromed to add corrosion resistance and improve aesthetic appearance, particularly useful in decorative applications.
- Iron: Chrome plating of iron provides a durable and shiny finish, making it suitable for a variety of industrial and decorative applications.
- Zinc alloys: Zinc alloys, such as zamak, can be chromed to improve their appearance and protect them from corrosion.
Chrome plating can be applied to many other types of metals as long as they are properly prepared for the coating process. However, the choice of metal will depend on the specific needs of the application and the desired properties of the finished product.
What are its characteristics?
Decorative chrome plating, glossy, matte or black, has these peculiarities:
- esthetically much appreciated;
- Excellent corrosion resistance;
- excellent abrasion resistance.
How does the Chrome Plating Process work?
Chrome plating is a meticulous process that transforms the surface of a metal, giving it a shiny, corrosion-resistant finish. It begins with thorough preparation of the surface, which is cleaned to remove any traces of dirt, grease, or corrosion that could compromise the final result. Then, in some cases, a layer of nickel is applied to improve the adhesion of the chromium coating and corrosion resistance.
The application of the chromium coating is done through an electrolytic or spray process. In electroplating, the part to be chromed is immersed in a solution containing chromium, acting as the cathode, while a chromium anode is present in the same solution. When an electric current is applied, chromium ions are reduced and deposited on the surface of the metal piece. In spray chromium plating, on the other hand, particles of chromium are sprayed onto the surface of the metal part and then melted by heating to form the coating.
After the chrome coating is applied, the surface is finished by polishing or sanding to achieve the desired finish, removing any imperfections. Finally, the part undergoes quality control to ensure that it meets the required standards in terms of coating adhesion, thickness, and aesthetic appearance.
This process requires great precision and attention to detail to achieve optimal results, both aesthetically and functionally.
How many types of chrome plating are there?
There are several types of chrome plating, each of which offers specific advantages depending on the needs of the application. Some of the main types of chrome plating include:
- Decorative chrome plating: This type of chrome plating is mainly aimed at improving the aesthetic appearance of metal materials. It is used to give a shiny, glossy finish to items such as automotive parts, furniture, home accessories and jewelry.
- Industrial chrome plating: Industrial chrome plating is designed to provide corrosion and wear protection in industrial and commercial environments. This type of chrome plating is often used on mechanical parts, industrial equipment, tools and electronic components.
- Hard chrome plating: This form of chrome plating, also known as hard chrome plating, employs a thick chrome coating to improve resistance to wear, abrasion and corrosion. It is commonly used on drive shafts, hydraulic cylinders, cutting tools and other surfaces subject to high mechanical stress.
- Black chrome plating: This process involves applying a black chromium oxide coating to metal surfaces, providing a dark, matte finish. Black chrome plating is often used for decorative purposes or to improve the lubrication and corrosion resistance properties of metal parts.
- Trivalent chromium plating: This form of chromium plating uses trivalent chromium compounds instead of hexavalent chromium, thus reducing the environmental impact and health risk associated with traditional chromium plating. Trivalent chromium plating still offers excellent corrosion and abrasion resistance and is increasingly used as a more sustainable alternative to hexavalent chromium plating.
These are just some of the main types of chrome plating, but there are also other specialized variations depending on the specific needs of the application.
What is the difference between electroplating and hot chromium plating?
Electroplating and hot chromium plating are two different methods of applying a chromium coating to a metal surface, and they differ mainly in the process used and the properties of the resulting coating.
Galvanic chromium plating, also known as electroplating, is a process that involves immersing the metal part to be chromed in an electrolyte solution containing chromium. In this process, the metal piece serves as the cathode and a chromium anode is immersed in the solution. When an electric current is applied, chromium ions in the solution are reduced and deposited on the surface of the metal piece, forming the chromium coating. This method is commonly used to achieve thin, uniform coatings that are ideal for decorative and protective applications.
On the other hand, hot chromium plating is a process in which the chromium coating is applied by casting to the surface of the metal part. During this process, a chromium alloy is melted and applied to the surface of the metal to be chromed by dipping or by a spraying process. The resulting coating is usually thicker and stronger than galvanic chrome plating, making it suitable for applications where greater resistance to wear and corrosion is required, such as mechanical components subject to high stresses.
Thus, the main difference between electroplating and hot chromium plating lies in the process of applying the chromium coating: while electroplating is done by an electrolytic process, hot chromium plating involves melting and directly applying chromium to the metal surface.
Metal chrome plating and decorative chrome plating represent two fundamental processes for improving the aesthetic appearance, strength, and durability of metal materials. Metal chrome plating offers solid protection from corrosion and wear, making metal components suitable for a wide range of industrial and commercial applications. On the other hand, decorative chrome plating goes beyond mere functionality, lending distinctive elegance and style to objects and surfaces, ranging from home furnishings to design products. Both processes involve meticulous attention to detail and strict quality control to ensure optimal results. The choice between metal chrome plating and decorative chrome plating depends on the specific needs of the application and the desired aesthetic goal, but both help to enhance and improve the appearance of metal materials in the industrial and design landscape.
Treatable materials
- Stainless steel
- Carbon steel
- Extruded aluminum / laminate
- Casting aluminum
- Iron
- Cast iron
- Brass
- Copper
- Zama
Standards and customer specifications
- UNI EN 12540
- UNI 6161
- UNI 4525
- UNI 9948
- UNI 4235
- UNI 8159
- BMW GS90010
- DBL 8459
- FIAT 9.57411
- FIAT 9.57410
- VW 13750
- TL 203
- PIAGGIO 2791
- GM9984001
Available finishes
- Polished chrome plating
- Satin chrome plating
- Pearl chrome plating
- Matt chrome plating
- Semi-gloss chrome plating
- Glossy black trivalent chrome plating
Maximum treatable size
2700 x 1200 x 500 mm
Treatable materials
- Stainless steel
- Carbon steel
- Extruded aluminum / laminate
- Casting aluminum
- Iron
- Cast iron
- Brass
- Copper
- Zama
Available finishes
- Polished chrome plating
- Satin chrome plating
- Pearl chrome plating
- Matt chrome plating
- Semi-gloss chrome plating
- Glossy black trivalent chrome plating
Standards and customer specifications
- UNI EN 12540
- UNI 6161
- UNI 4525
- UNI 9948
- UNI 4235
- UNI 8159
- BMW GS90010
- DBL 8459
- FIAT 9.57411
- FIAT 9.57410
- VW 13750
- TL 203
- PIAGGIO 2791
- GM9984001
Maximum treatable size
2700 x 1200 x 500 mm
Sectors
implementing
implementing
Application areas
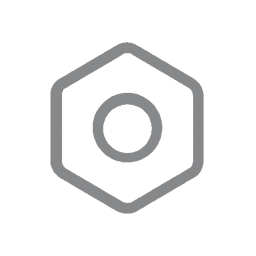
Minutery
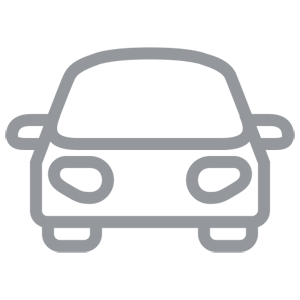
Automotive
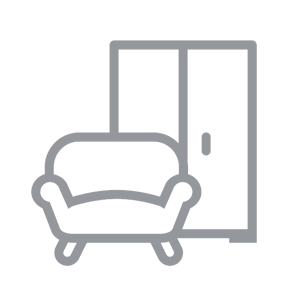
Furniture
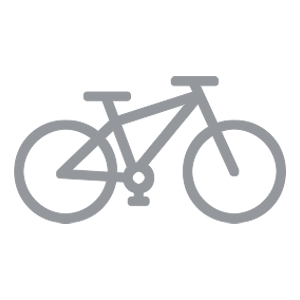
Cycle
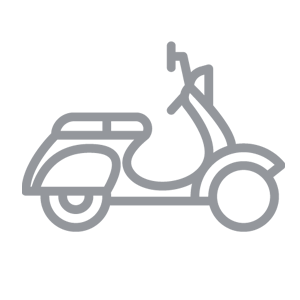
Motorcycle
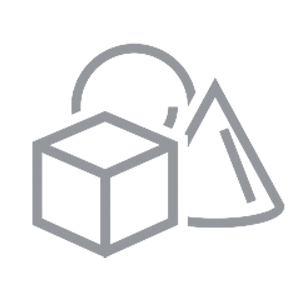
Objects
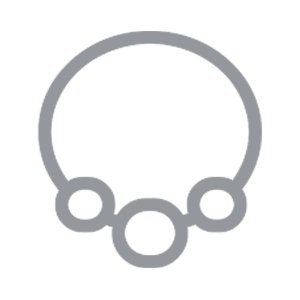
Accessories
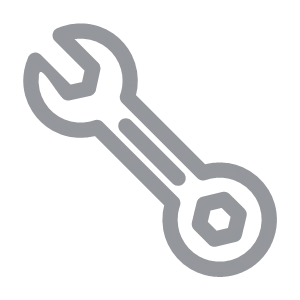