Decorative treatments
RAMATURA
Decorative treatments
Coppering
Enhancing Durability and Reliability: The Crucial Role of Metal Plating
Metal plating is a surface treatment process that is used to improve the mechanical, chemical and physical properties of metals. This process involves applying a protective layer of metal to a base metal surface through various techniques, such as electroplating, electrodeposition, sputtering or chemical vapor deposition. The main objective of copper plating is to provide protection against corrosion, wear, abrasion, and other environmental damage, thereby improving the durability and reliability of the treated metal. In addition, copper plating can also be used for aesthetic purposes, giving the metal a more attractive and bright finish. This process is widely used in a wide range of industries, including automotive, aerospace, electronics, construction, and many others, where the strength and appearance of the metal are critical to the performance and aesthetics of the final product.
What is it for
coppering?
Copper plating of metals serves several purposes:
- Corrosion protection: One of the main uses of copper plating is to protect metals from atmospheric, chemical or electrochemical corrosion. The protective layer applied during the coppering process acts as a barrier between the base metal and the surrounding environment, thus preventing rust or other corrosive damage.
- Wear and abrasion resistance: Copper plating can improve the resistance of the treated metal to wear and abrasion, thus extending its service life and durability. This is especially important in applications where the metal is subject to mechanical stress or in contact with abrasive materials.
- Improved surface properties: Copper plating can improve metal surface properties, such as hardness, tensile strength, fatigue strength, and thermal stress resistance, making it more suitable for specific applications or operating environments.
- Aesthetic enhancement: In many cases, copper plating is also used to improve the aesthetic appearance of metal, giving it a brighter, more uniform or decorative finish. This is especially important in industries such as automotive, furniture and the high-fashion industry, where the aesthetic appearance of metal is crucial to the attractiveness of the final product.
In summary, metal plating is a versatile process that offers a number of benefits, including corrosion protection, wear resistance, improved surface properties, and aesthetic enhancement, thus helping to improve the performance and reliability of metal products in a wide range of industrial and commercial applications.
Electroplating
Electroplating is a metal surface treatment process that involves immersing a metal object in an electrolyte solution containing metal ions. During this process, a potential difference is applied between the object to be treated, called the cathode, and an anode composed of a sacrificial metal or appropriate conductive material. The application of electric current induces the migration of metal ions from the electrolyte solution to the cathode surface, where they are deposited, forming a protective metal layer.
This metal layer can have different properties depending on process conditions, including thickness, hardness, adhesion and chemical composition. Electroplating can be used for a variety of purposes, including corrosion protection, improvement of the mechanical and aesthetic properties of the metal, and preparation of the surface for further treatment or coating. It is a process widely used in the manufacturing industry to improve the performance and reliability of metal components in a wide range of applications.
How does the process take place?
The oxide that is formed is not due to material input but to a transformation of the original surface of the object. The aluminum surface undergoing anodizing is progressively oxidized from the outside of the surface progressing inward. The ‘oxide that is formed has a larger volume than the original metal (aluminum) so that apparently, from a dimensional point of view, it seems away is a material contribution, in reality the thickness of oxide partly “penetrates” into the metal partly “grows” outward. In practice for a thickness of e.g. 10 microns, 5 microns penetrated and 5 microns expanded so the geometric increase amounts to 5 microns. Note that, on a diameter, the 10-micron thickness produces an increase in diameter of 10 microns, not 20.
Oxide also tends to form fairly uniformly in recesses, undercuts, and inside pipes. The structure of the oxide is very similar to the “honeycomb” structure with vertical tubules with respect to the thickness formed. These tubules are much less than a micron in diameter, but particular dyes can penetrate them, being able to impart a wide variety of colorations to the oxide layer. Following the formation of the oxide layer and, eventual staining, a pore-closing operation is performed in order to ensure compactness and corrosion resistance. This operation is called fixing and can be done cold or hot. in any case, the pores are closed; however, it turns out to be safer to heat fix especially for colored oxide layers.
Enhancing Durability and Reliability: The Crucial Role of Metal Plating
Metal plating is a surface treatment process that is used to improve the mechanical, chemical, and physical properties of metals. This process involves applying a protective layer of metal to a base metal surface through various techniques, such as electroplating, electrodeposition, sputtering or chemical vapor deposition. The main objective of copper plating is to provide protection against corrosion, wear, abrasion, and other environmental damage, thereby improving the durability and reliability of the treated metal. In addition, copper plating can also be used for aesthetic purposes, giving the metal a more attractive and bright finish. This process is widely used in a wide range of industries, including automotive, aerospace, electronics, construction, and many others, where the strength and appearance of the metal are critical to the performance and aesthetics of the final product.
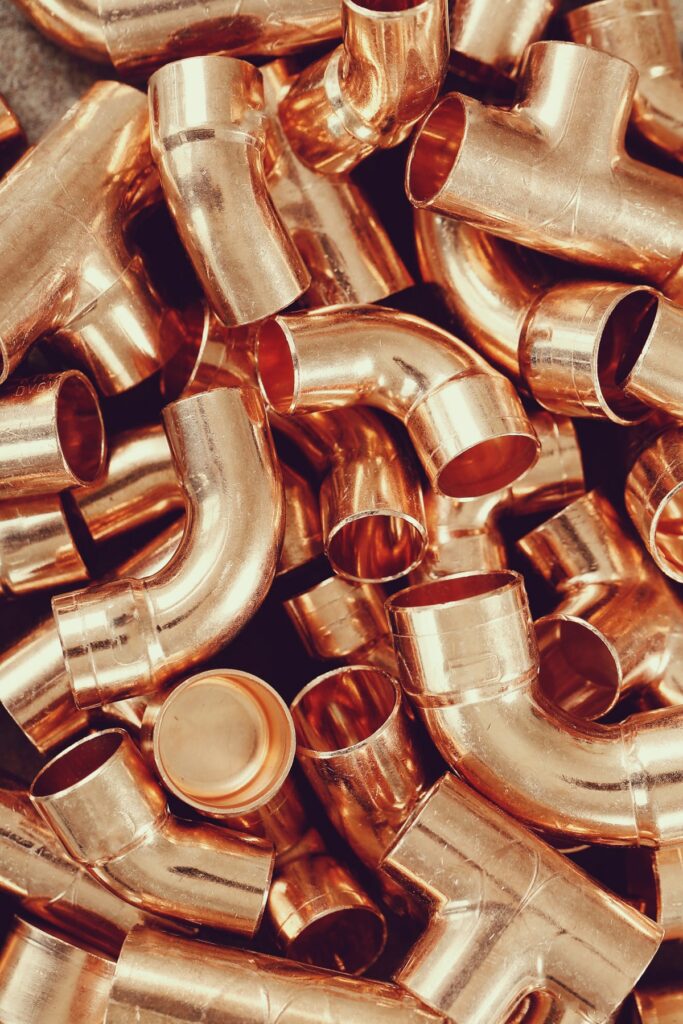
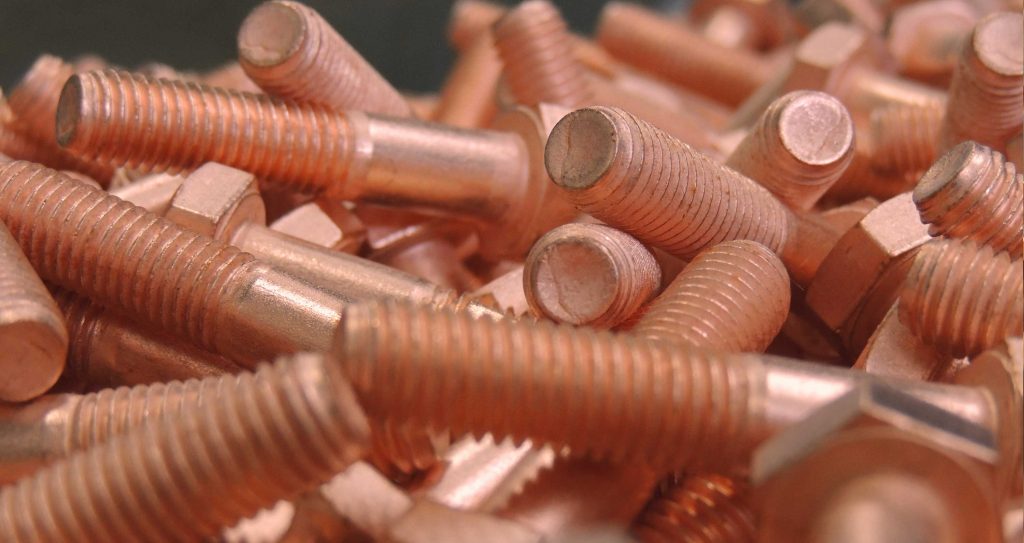
What Copper Plating Is For
What is the purpose of coppering?
Copper plating of metals serves several purposes:
- Corrosion protection: One of the main uses of copper plating is to protect metals from atmospheric, chemical or electrochemical corrosion. The protective layer applied during the coppering process acts as a barrier between the base metal and the surrounding environment, thus preventing rust or other corrosive damage.
- Wear and abrasion resistance: Copper plating can improve the resistance of the treated metal to wear and abrasion, thus extending its service life and durability. This is especially important in applications where the metal is subject to mechanical stress or in contact with abrasive materials.
- Improved surface properties: Copper plating can improve metal surface properties, such as hardness, tensile strength, fatigue strength, and thermal stress resistance, making it more suitable for specific applications or operating environments.
- Aesthetic enhancement: In many cases, copper plating is also used to improve the aesthetic appearance of metal, giving it a brighter, more uniform or decorative finish. This is especially important in industries such as automotive, furniture and the high-fashion industry, where the aesthetic appearance of metal is crucial to the attractiveness of the final product.
In summary, metal plating is a versatile process that offers a number of benefits, including corrosion protection, wear resistance, improved surface properties, and aesthetic enhancement, thus helping to improve the performance and reliability of metal products in a wide range of industrial and commercial applications.
CONTACT US!
Electroplating
Electroplating is a metal surface treatment process that involves immersing a metal object in an electrolyte solution containing metal ions. During this process, a potential difference is applied between the object to be treated, called the cathode, and an anode composed of a sacrificial metal or appropriate conductive material. The application of electric current induces the migration of metal ions from the electrolyte solution to the cathode surface, where they are deposited, forming a protective metal layer.
This metal layer can have different properties depending on process conditions, including thickness, hardness, adhesion and chemical composition. Electroplating can be used for a variety of purposes, including corrosion protection, improvement of the mechanical and aesthetic properties of the metal, and preparation of the surface for further treatment or coating. It is a process widely used in the manufacturing industry to improve the performance and reliability of metal components in a wide range of applications.
How does the process take place?
The oxide that is formed is not due to material input but to a transformation of the original surface of the object. The aluminum surface undergoing anodizing is progressively oxidized from the outside of the surface progressing inward. The ‘oxide that is formed has a larger volume than the original metal (aluminum) so that apparently, from a dimensional point of view, it seems away is a material contribution, in reality the thickness of oxide partly “penetrates” into the metal partly “grows” outward. In practice for a thickness of e.g. 10 microns, 5 microns penetrated and 5 microns expanded so the geometric increase amounts to 5 microns. Note that, on a diameter, the 10-micron thickness produces an increase in diameter of 10 microns, not 20.
Oxide also tends to form fairly uniformly in recesses, undercuts, and inside pipes. The structure of the oxide is very similar to the “honeycomb” structure with vertical tubules with respect to the thickness formed. These tubules are much less than a micron in diameter, but particular dyes can penetrate them, being able to impart a wide variety of colorations to the oxide layer. Following the formation of the oxide layer and, eventual staining, a pore-closing operation is performed in order to ensure compactness and corrosion resistance. This operation is called fixing and can be done cold or hot. in any case, the pores are closed; however, it turns out to be safer to heat fix especially for colored oxide layers.
Chemical Copper Plating
Chemical copper plating is a metal surface treatment process that occurs by immersing the metal object in a specifically formulated chemical solution. During this process, the surface of the metal reacts with the chemicals in the solution, forming a protective layer on the surface of the object.
This chemical reaction can result in the formation of compounds that improve metal properties, such as resistance to corrosion, wear, or high temperatures. The composition and conditions of the chemical solution are carefully controlled to achieve the desired effects and ensure uniform treatment on the metal surface.
Chemical copper plating is used in various industries to improve the performance and reliability of metal components, and is particularly suitable for objects with complex shapes or for materials sensitive to temperature or corrosion. It is an effective and cost-effective process for achieving uniform and long-lasting surface protection on metals.
Chemical copper plating is a metal surface treatment process that occurs by immersing the metal object in a specifically formulated chemical solution. During this process, the surface of the metal reacts with the chemicals in the solution, forming a protective layer on the surface of the object.
This chemical reaction can result in the formation of compounds that improve metal properties, such as resistance to corrosion, wear, or high temperatures. The composition and conditions of the chemical solution are carefully controlled to achieve the desired effects and ensure uniform treatment on the metal surface.
Chemical copper plating is used in various industries to improve the performance and reliability of metal components, and is particularly suitable for objects with complex shapes or for materials sensitive to temperature or corrosion. It is an effective and cost-effective process for achieving uniform and long-lasting surface protection on metals.
Alkaline Copper Plating
Alkaline plating is a metal surface treatment process that involves immersing the metal object in an alkaline solution containing chemicals such as sodium or potassium hydroxides. During this process, the alkaline solution reacts with the metal surface, forming a protective layer of metal oxides or hydroxides on its substrate.
This chemical reaction changes the surface of the metal, giving it improved properties such as corrosion resistance and adhesion of subsequent coatings. Alkaline copper plating is particularly effective for cleaning and preparing metal surfaces before applying protective or decorative coatings.
One of the main advantages of alkaline plating is its ability to effectively remove oils, grease, machining residues and other contaminants from the metal surface, thereby improving the adhesion of subsequent coatings and providing longer-lasting protection.
Alkaline copper plating is widely used in industries such as automotive, aerospace, electronics, and industrial equipment manufacturing, where protecting metals against corrosion and wear is critical to the durability and performance of end products.
Alkaline plating is a metal surface treatment process that involves immersing the metal object in an alkaline solution containing chemicals such as sodium or potassium hydroxides. During this process, the alkaline solution reacts with the metal surface, forming a protective layer of metal oxides or hydroxides on its substrate.
This chemical reaction changes the surface of the metal, giving it improved properties such as corrosion resistance and adhesion of subsequent coatings. Alkaline copper plating is particularly effective for cleaning and preparing metal surfaces before applying protective or decorative coatings.
One of the main advantages of alkaline plating is its ability to effectively remove oils, grease, machining residues and other contaminants from the metal surface, thereby improving the adhesion of subsequent coatings and providing longer-lasting protection.
Alkaline copper plating is widely used in industries such as automotive, aerospace, electronics, and industrial equipment manufacturing, where protecting metals against corrosion and wear is critical to the durability and performance of end products.
The coppering of Iron
Iron plating is a surface treatment process aimed at protecting iron from corrosion and wear. This method involves applying a protective layer to the surface of iron through techniques such as electroplating, painting or chemical coppering.
One of the most common methods for coppering iron is galvanization, which involves immersing iron in a molten zinc solution or an electrolyte solution containing zinc ions. During the process, zinc ions are deposited on the surface of the iron, forming a layer of zinc metal that protects the iron from corrosion. This zinc layer provides a physical barrier between the iron and the surrounding environment, preventing rusting and extending the useful life of the material.
Other iron coppering techniques include painting with galvanized primer or applying protective coatings based on epoxy or polyurethane resins. These coatings provide additional protection against corrosion and wear, protecting iron even in aggressive or weathered environments.
In summary, iron plating is an essential process for ensuring the durability and strength of the material, protecting it from corrosion and wear and extending its useful life in a variety of industrial and commercial applications.
Do you need help?
What is Thick Coppering
Thick copper plating is a metal surface treatment process that involves applying a significant layer of protective material to the metal surface. Unlike other coppering methods that create a thin, uniform layer, thick coppering is characterized by the deposition of a thicker layer of protective material.
This process is usually used when more robust protection against corrosion, wear and tear, or other environmental damage is needed. Thick coppering can be achieved through various methods, including hot dip galvanization, where the base metal is fully immersed in a bath of molten metal, such as zinc or aluminum, forming a thick, uniform layer on its surface.
Other methods of achieving thick coppering include chemical vapor deposition (CVD) and physical vapor deposition (PVD), which allow a thick layer of protective material to be applied using vacuum deposition processes.
Thick copper plating is commonly used in industries such as mechanical component manufacturing, the shipbuilding industry, infrastructure construction, and other applications where strong and durable protection against the aggressive environment is required.
Metal coppering represents an essential and versatile process in metal materials processing. Through the application of protective layers on the surface of metals, coppering offers a number of significant benefits, including corrosion protection, increased mechanical strength, improved durability and aesthetics.
Whether electrolytic, chemical, alkaline coppering or other methods, each technique has its specific role and preferred applications, allowing treatment to be tailored to the specific needs of the material and end application.
In a world where product reliability and longevity are increasingly crucial, metal plating is confirmed as an important resource for ensuring the quality and performance of metal components in a wide range of industries. Continued research and development in the field of metal plating promises to further improve this technology, enabling it to meet emerging needs and anticipate future challenges in the metal processing industry.
do you need help?
Treatable materials
- Carbon steel
- Iron
- Stainless steel
- Copper
- Brass
- Aluminum
Regulations
- UNI ISO 6158
- UNI 5082
Possible finishes
- White passivation (chrome 3)
- High strength passivation (chrome 3)
- Black passivation (chrome 3)
Maximum treatable size
2700x500x1200 mm
Treatable materials
- Iron
- Copper
- Brass
- Aluminum
Possible finishes
- White passivation (chrome 3)
- High strength passivation (chrome 3)
- Black passivation (chrome 3)
Regulations
- UNI ISO 6158
- UNI 5082
Maximum treatable size
2700x500x1200 mm
Sectors
implementing
implementing
Application areas
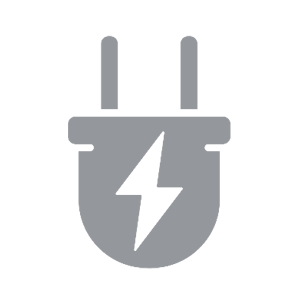
Electrotechnician
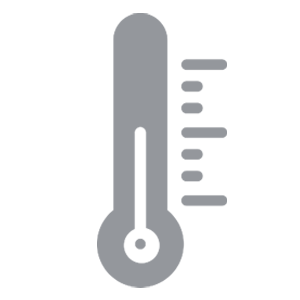
Thermotechnician
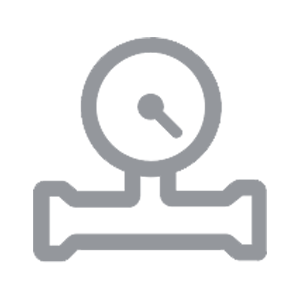
Fittings
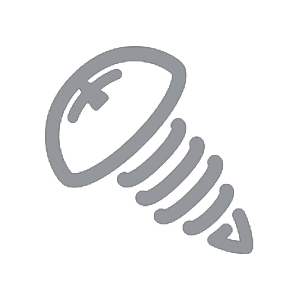