Protective treatments
Zinc aluminum lamellar
Protective treatments
Zinc aluminum lamellar
Protective treatments: the aluminum zinc lamellar
What is zinc aluminum foil?
Laminated aluminum zinc is a coating consisting of micro flakes of aluminum and zinc, a few microns in size, each protected with its own passivation, which are applied to the surface of the objects to be protected and brought to the temperature on them that allows microfusion of the flakes with each other and rooting to the base material. The version just described is water-based and all the carryover is mineral and is the most effective version with the least thickness. There are solvent-based versions where the metal flakes of zinc and aluminum remain in an organic matrix that is spread over the materials to be protected. In any case, the protective function occurs cathodically ( as with galvanizing) in the sense that the carryover functions as an anode by melting, imparting protection to the base material (cathode). The high protection achieved is due to the fact that the flakes form several layers, in the sense of thickness. Corrosion, proceeding from the outside to the inside, once the first sliver is corroded is likely to stop. Note that unlike electrolytic galvanizing, where the deposited zinc layer has only a passivation on the outside, in the case of aluminum flake zinc each individual flake is protected by its own form of passivation.
All operations associated with the product application cycle are non-hydrogenating so, unlike other galvanizing treatments, aluminum zinc flake coatings are not hydrogenating.
How is it realized?
The material to be coated with laminated aluminum zinc should be degreased and stripped of any possible oxidation. For this purpose, the parts are washed in solvent or water-based detergents. Sandblasting is performed to remove oxides. This operation is preferred in place of the usual pickling in order not to introduce hydrogenating steps in a process that is free of them, this to great advantage for the protective treatment of all safety organs.
Once the preparation is done, the product containing the zinc and aluminum is applied. This product looks like a very metallic paint and like it must be kept in constant motion to avoid settling. Parameters such as temperature, viscosity, dry residue and other specifics must be controlled in this suspension ( which can be water- or solvent-based). Application of the product can be by immersion and centrifugation (mass) or by spraying. After application, the parts are baked for at least 30 minutes at temperatures that, depending on the specific product, can range from 220 to 320°C. Once the parts have cooled, if mass-treated they typically undergo a second round of product application to cover previously uncovered spots. If spray-treated, they are ready for packaging.
Other products can be applied, to increase corrosion resistance, to achieve specific coloration, or to impart predetermined coefficient of friction, especially to hardware. It is also possible to obtain predetermined coefficients of friction by applying zinc aluminum foil that already contains a friction coefficient corrector.
How does the process take place?
The oxide that is formed is not due to material input but to a transformation of the original surface of the object. The aluminum surface undergoing anodizing is progressively oxidized from the outside of the surface progressing inward. The ‘oxide that is formed has a larger volume than the original metal (aluminum) so that apparently, from a dimensional point of view, it seems away is a material contribution, in reality the thickness of oxide partly “penetrates” into the metal partly “grows” outward. In practice for a thickness of e.g. 10 microns, 5 microns penetrated and 5 microns expanded so the geometric increase amounts to 5 microns. Note that, on a diameter, the 10-micron thickness produces an increase in diameter of 10 microns, not 20.
Oxide also tends to form fairly uniformly in recesses, undercuts, and inside pipes. The structure of the oxide is very similar to the “honeycomb” structure with tubules vertical to the thickness formed. These tubules are much less than a micron in diameter, but particular dyes can penetrate them, being able to impart a wide variety of colorations to the oxide layer. Following the formation of the oxide layer and, eventual staining, a pore-closing operation is performed in order to ensure compactness and corrosion resistance. This operation is called fixing and can be done cold or hot. in any case, the pores are closed; however, it turns out to be safer to heat fix especially for colored oxide layers.
Protective treatments: the zinc aluminum lamellar
What is zinc aluminum foil?
Laminated aluminum zinc is a coating consisting of micro flakes of aluminum and zinc, a few microns in size, each protected with its own passivation, which are applied to the surface of the objects to be protected and brought to the temperature on them that allows microfusion of the flakes with each other and rooting to the base material. The version just described is water-based and all the carryover is mineral and is the most effective version with the least thickness. There are solvent-based versions where the metal flakes of zinc and aluminum remain in an organic matrix that is spread over the materials to be protected. In any case, the protective function occurs cathodically ( as with galvanizing) in the sense that the carryover functions as an anode by melting, imparting protection to the base material (cathode). The high protection achieved is due to the fact that the flakes form several layers, in the sense of thickness. Corrosion, proceeding from the outside to the inside, is likely to stop once the first sliver is corroded. Note that unlike electrolytic galvanizing, where the deposited zinc layer has only a passivation on the outside, in the case of aluminum flake zinc each individual flake is protected by its own form of passivation.
All operations associated with the product application cycle are non-hydrogenating so, unlike other galvanizing treatments, aluminum zinc flake coatings are not hydrogenating.
How is it realized?
The material to be coated with laminated aluminum zinc should be degreased and stripped of any possible oxidation. For this purpose, the parts are washed in solvent or water-based detergents. Sandblasting is performed to remove oxides. This operation is preferred in place of the usual pickling in order not to introduce hydrogenating steps in a process that is free of them, this to great advantage for the protective treatment of all safety organs.
Once the preparation is done, the product containing the zinc and aluminum is applied. This product looks like a very metallic paint and like it must be kept in constant motion to avoid settling. Parameters such as temperature, viscosity, dry residue and other specifics must be controlled in this suspension ( which can be water or solvent based). Application of the product can be by immersion and centrifugation (mass) or by spraying. After application, the parts are baked for at least 30 minutes at temperatures that, depending on the specific product, can range from 220 to 320°C. Once the parts have cooled, if mass-treated they typically undergo a second round of product application to cover previously uncovered spots. If spray-treated, they are ready for packaging.
Other products can be applied, to increase corrosion resistance, to achieve specific coloration, or to impart predetermined coefficient of friction, especially to hardware. It is also possible to achieve predetermined coefficients of friction by applying zinc aluminum foil that already contains a friction coefficient corrector.
How does the process take place?
The oxide that is formed is not due to material input but to a transformation of the original surface of the object. The aluminum surface undergoing anodizing is progressively oxidized from the outside of the surface progressing inward. The ‘oxide that is formed has a larger volume than the original metal (aluminum) so that apparently, from a dimensional point of view, it seems away is a material contribution, in reality the thickness of oxide partly “penetrates” into the metal partly “grows” outward. In practice for a thickness of e.g. 10 microns, 5 microns penetrated and 5 microns expanded so the geometric increase amounts to 5 microns. Note that, on a diameter, the 10-micron thickness produces an increase in diameter of 10 microns, not 20.
Oxide also tends to form fairly uniformly in recesses, undercuts, and inside pipes. The structure of the oxide is very similar to the “honeycomb” structure with vertical tubules with respect to the thickness formed. These tubules are much less than a micron in diameter, but particular dyes can penetrate them, being able to impart a wide variety of colorations to the oxide layer. Following the formation of the oxide layer and, eventual staining, a pore-closing operation is performed in order to ensure compactness and corrosion resistance. This operation is called fixing and can be done cold or hot. in any case, the pores are closed; however, it turns out to be safer to heat fix especially for colored oxide layers.
Treatable materials
- Carbon steel
- Iron
- AVP, AVZ
- C40, C45, Fe, 8.8, 10.9, 12.9,
- Aluminum, 2011, 11S, 6060, 6082, 7075
- Die-cast aluminum
- Cast iron
- Sintered ferrous
Regulations
- UNI EN ISO 10683
- UNI 3740/6
Possible finishes
- White passivation (chrome 3)
- High strength passivation (chrome 3)
- Black passivation (chrome 3)
Maximum treatable size
2,450 x 500 x 1,000 mm
Treatable materials
- Carbon steel
- Iron
- AVP, AVZ
- C40, C45, Fe, 8.8, 10.9, 12.9,
- Aluminum, 2011, 11S, 6060, 6082, 7075
- Die-cast aluminum
- Cast iron
- Sintered ferrous
Possible finishes
- White passivation (chrome 3)
- High strength passivation (chrome 3)
- Black passivation (chrome 3)
Regulations
- UNI EN ISO 10683
- UNI 3740/6
Maximum treatable size
2,450 x 500 x 1,000 mm
Sectors
implementing
implementing
Application areas
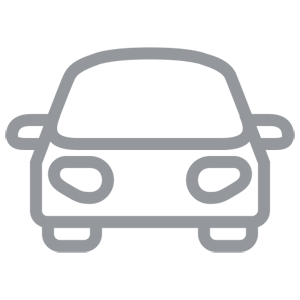
Automotive
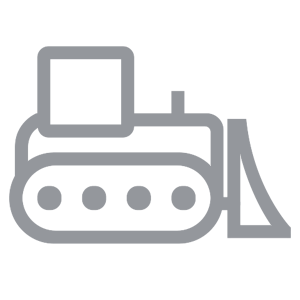
Earthmoving
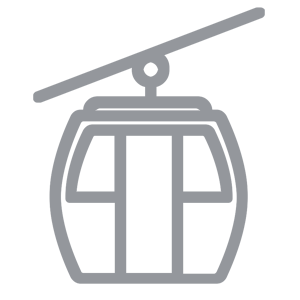
Cable cars
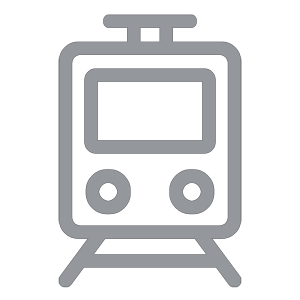
Railway
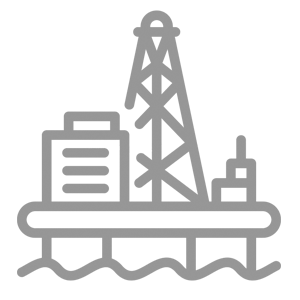
Offshore
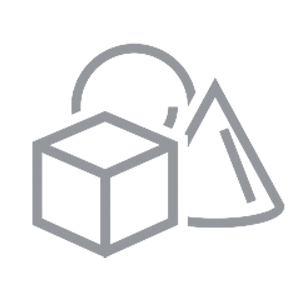
Thermotechnician
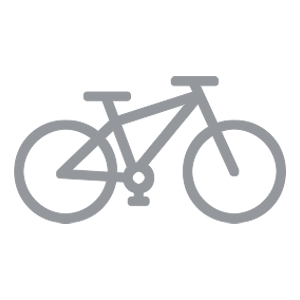
Fittings
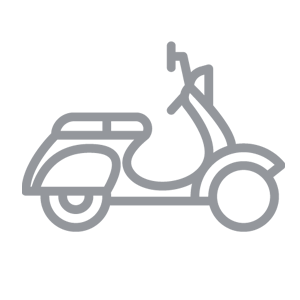