Trattamenti funzionali
Argentatura tecnica
Trattamenti funzionali
Argentatura tecnica
Trattamenti funzionali: l'argentatura tecnica
Cos’è l’argentatura tecnica?
L’argentatura è un processo elettrolitico di deposizione di argento per sfruttarne le caratteristiche di conducibilità elettrica e di bassa resistenza di contatto.
Le specifiche dei clienti più comuni prevedono depositi da 0,5 a 10 micron, ma in alcuni casi applichiamo spessori anche di 50 micron. Per minuteria disponiamo dell’argentatura a rotobarile, per particolari di maggiori dimensioni o dove si voglia preservare l’estetica o la superficie del pezzo disponiamo di un impianto a telaio.
L’aspetto estetico è un bianco brillante caratteristico dell’argentatura elettrolitica tecnica, diverso dal “silver plated” che invece risulta essere solamente una finitura estetica.
Tipologie di Argentatura
L’argentatura dei metalli può essere realizzata attraverso diverse tecniche, ognuna delle quali offre vantaggi specifici in termini di precisione, uniformità del rivestimento e adattabilità alle esigenze del manufatto. Le tecniche principali includono:
- Argentatura elettrolitica: Questa è la tecnica più comune e impiega un processo elettrolitico per depositare uno strato uniforme di argento sulla superficie del metallo. Viene utilizzata una soluzione elettrolitica contenente ioni di argento, che vengono depositati sulla superficie del metallo mediante l’applicazione di corrente elettrica. Questo metodo permette un controllo preciso dello spessore del rivestimento e garantisce una distribuzione uniforme dell’argento.
- Argentatura chimica: Questo metodo coinvolge l’utilizzo di sostanze chimiche che reagiscono con la superficie del metallo, creando uno strato di argento sulla sua superficie. Questa tecnica è spesso impiegata per rivestimenti meno uniformi o in situazioni in cui l’argentatura elettrolitica non è praticabile.
- Argentatura al fuoco: Questo processo prevede l’applicazione di un sottile strato di polvere di argento sulla superficie del metallo, seguito da un trattamento termico che fonde la polvere, formando uno strato uniforme di argento sulla superficie del pezzo. Questa tecnica è particolarmente adatta per metalli ad alta temperatura di fusione.
- Argentatura mediante immersione: Questa tecnica coinvolge l’immersione del pezzo metallico in una soluzione contenente particelle di argento sospese in una soluzione chimica. Le particelle di argento aderiscono alla superficie del metallo per adesione chimica o meccanica.
Cosa si intende per argentatura galvanica ?
L’argentatura galvanica, nota anche come argentatura elettrolitica, è un processo mediante il quale uno strato di argento viene depositato su un metallo di base tramite un’azione elettrochimica controllata. Questo metodo sfrutta i principi dell’elettrolisi, dove un’anodo costituito da argento e un catodo costituito dal metallo da argentare vengono immersi in una soluzione elettrolitica contenente ioni di argento. Quando viene applicata una corrente elettrica, gli ioni di argento si riducono sulla superficie del metallo da argentare, formando uno strato di argento uniforme.
L’argentatura galvanica offre diversi vantaggi, tra cui la capacità di depositare uno strato uniforme di argento su superfici complesse e irregolari, il controllo preciso dello spessore del rivestimento e la resistenza alla corrosione migliorata del metallo di base. Questo processo è ampiamente utilizzato in una vasta gamma di settori industriali per migliorare l’estetica, la conducibilità elettrica e le proprietà anticorrosive dei manufatti metallici.
Cosa si intende per argentatura a freddo?
L’argentatura a freddo è un metodo alternativo per depositare uno strato di argento su una superficie metallica senza utilizzare il calore. A differenza dell’argentatura galvanica, che coinvolge un processo elettrolitico controllato, l’argentatura a freddo si basa su una reazione chimica tra una soluzione contenente ioni di argento e la superficie del metallo da trattare.
Nel processo di argentatura a freddo, la soluzione contenente ioni di argento viene applicata direttamente sulla superficie del metallo mediante immersione, pennellatura o spruzzatura. Gli ioni di argento presenti nella soluzione reagiscono con la superficie del metallo, depositando uno strato sottile di argento. Questo processo è solitamente più lento e meno controllabile rispetto all’argentatura galvanica, ma può essere utilizzato in situazioni in cui l’uso del calore è indesiderato o non praticabile.
L’argentatura a freddo può essere impiegata per scopi decorativi, funzionali o protettivi, a seconda delle esigenze specifiche del manufatto e del processo applicativo. Tuttavia, è importante notare che questo metodo potrebbe non garantire la stessa uniformità e resistenza della argentatura galvanica, soprattutto in termini di spessore e aderenza dello strato di argento.
Cosa si intende per argentatura a spessore?
L’argentatura a spessore si riferisce a un processo di argentatura in cui viene depositato uno strato relativamente più spesso di argento sulla superficie di un oggetto metallico. Questo strato di argento può essere significativamente più spesso rispetto alla normale argentatura elettrolitica o chimica, che solitamente produce uno strato di argento molto sottile.
Nel caso dell’argentatura a spessore, il rivestimento di argento può essere applicato mediante varie tecniche, tra cui l’argentatura galvanica o elettroless, in cui viene utilizzato un processo chimico per depositare lo strato di argento sulla superficie del metallo di base.
L’argentatura a spessore può essere richiesta per una serie di motivi, tra cui:
- Requisiti di resistenza e durabilità: Uno strato più spesso di argento può fornire una maggiore resistenza all’usura e alla corrosione, rendendo il pezzo più durevole nel tempo.
- Proprietà estetiche: Uno strato più spesso di argento può creare un aspetto più brillante e riflettente, migliorando l’estetica del pezzo e conferendogli un valore aggiunto.
- Requisiti funzionali: In alcune applicazioni, uno spessore maggiore di argento può essere necessario per garantire una migliore conducibilità elettrica o termica
Quanto costa fare il bagno d’argento?
Il costo per fare il bagno d’argento dipende da diversi fattori che possono influenzare il costo complessivo del processo. Alcuni dei principali fattori includono:
- Dimensioni e complessità del pezzo: Pezzi più grandi o più complessi possono richiedere più tempo e risorse per essere trattati, influenzando il costo complessivo del bagno d’argento.
- Tipo di metallo di base: Alcuni metalli possono richiedere trattamenti pre-bagno o condizioni speciali per l’argentatura, il che può influenzare i costi.
- Spessore del rivestimento: Il costo può variare a seconda dello spessore di argento richiesto sul pezzo. Maggiore è lo spessore richiesto, maggiore sarà il consumo di materiale argentato e, di conseguenza, maggiore sarà il costo.
- Metodo di argentatura: Tecniche diverse, come l’argentatura galvanica, l’argentatura chimica o altre varianti, possono avere costi di materiale e di lavoro diversi.
- Quantità: Il costo unitario può diminuire all’aumentare della quantità di pezzi da trattare, grazie a economie di scala nel processo di produzione.
- Finitura e specifiche richieste: Se sono richieste finiture speciali o specifiche aggiuntive, come lucidatura, pulizia o controlli di qualità, ciò può influenzare i costi.
- Localizzazione del servizio: Il costo può variare a seconda della regione geografica in cui viene eseguito il bagno d’argento, a causa delle differenze nei costi della manodopera e dei materiali.
- Requisiti ambientali e normative: Se il processo deve essere conforme a determinati standard ambientali o normative, ciò potrebbe comportare costi aggiuntivi per l’implementazione di tecnologie o pratiche specifiche.
Come avviene il processo?
L’ossido che si forma non è dovuto ad un apporto di materiale ma ad una trasformazione della superficie originale dell’oggetto. La superficie di alluminio sottoposta ad anodizzazione viene ossidata progressivamente dall’esterno della superficie progredendo verso l’interno. L’ ossido che si forma ha un volume maggiore del metallo (alluminio) originario per cui apparentemente, dal punto di vista dimensionale, sembra via sia un apporto di materiale, in realtà lo spessore di ossido in parte “penetra” nel metallo in parte “cresce” verso l’esterno. In pratica per uno spessore di es. 10 micron, 5 micron sono penetrati e 5 micron si sono espansi per cui l’aumento geometrico ammonta a 5 micron. Da notare che, su un diametro, lo spessore di 10 micron produce un aumento del diametro pari a 10 micron e non 20.
L’ossido tende a formarsi abbastanza uniformemente anche nei recessi, nei sottosquadra, all’interno di tubi. La struttura dell’ossido è molto simile alla struttura del “nido d’ape” con tubuli verticali rispetto allo spessore formato. Questi tubuli hanno un diametro molto inferiore al micron, ma particolari coloranti vi possono penetrare, potendo conferire allo strato di ossido una grande varietà di colorazioni. Successivamente alla formazione dello strato di ossido e, alla eventuale colorazione, viene eseguita una operazione di chiusura dei pori al fine di garantire compattezza e resistenza alla corrosione. Questa operazione prende il nome di fissaggio e può avvenire a freddo o a caldo. in ogni caso i pori vengono chiusi, risulta tuttavia più sicura l’operazione di fissaggio a caldo soprattutto per gli strati di ossido colorato.
Trattamenti funzionali: l'argentatura tecnica
Cos’è l’argentatura tecnica?
L’argentatura è un processo elettrolitico di deposizione di argento per sfruttarne le caratteristiche di conducibilità elettrica e di bassa resistenza di contatto.
Le specifiche dei clienti più comuni prevedono depositi da 0,5 a 10 micron, ma in alcuni casi applichiamo spessori anche di 50 micron. Per minuteria disponiamo dell’argentatura a rotobarile, per particolari di maggiori dimensioni o dove si voglia preservare l’estetica o la superficie del pezzo disponiamo di un impianto a telaio.
L’aspetto estetico è un bianco brillante caratteristico dell’argentatura elettrolitica tecnica, diverso dal “silver plated” che invece risulta essere solamente una finitura estetica.
Rappresenta un fondamentale processo elettrolitico di deposizione di argento, mirato a sfruttarne le peculiari proprietà di conducibilità elettrica e bassa resistenza di contatto.
Questo trattamento funzionale, che si distingue per la sua versatilità e precisione, è ampiamente impiegato in una vasta gamma di settori industriali per conferire prestazioni ottimali e un’elevata estetica ai componenti elettronici e meccanici.
Questo processo può essere eseguito mediante diverse metodologie, tra cui l’argentatura a rotobarile per minuteria e l’utilizzo di impianti a telaio per particolari di maggiori dimensioni, dove è essenziale preservare l’estetica e la superficie del pezzo. L’aspetto estetico distintivo, caratterizzato da un bianco brillante, conferisce un valore aggiunto ai manufatti trattati con l’argentatura elettrolitica tecnica, che si distingue nettamente dal semplice “silver plated”, il quale si limita a una finitura puramente estetica, senza conferire le stesse proprietà funzionali e durature. In questa prospettiva, esploriamo l’essenza e l’importanza dell’argentatura tecnica, focalizzandoci sulle sue applicazioni, benefici e impatti nell’ambito industriale moderno.
Tipologie di Argentatura
L’argentatura dei metalli può essere realizzata attraverso diverse tecniche, ognuna delle quali offre vantaggi specifici in termini di precisione, uniformità del rivestimento e adattabilità alle esigenze del manufatto. Le tecniche principali includono:
- Argentatura elettrolitica: Questa è la tecnica più comune e impiega un processo elettrolitico per depositare uno strato uniforme di argento sulla superficie del metallo. Viene utilizzata una soluzione elettrolitica contenente ioni di argento, che vengono depositati sulla superficie del metallo mediante l’applicazione di corrente elettrica. Questo metodo permette un controllo preciso dello spessore del rivestimento e garantisce una distribuzione uniforme dell’argento.
- Argentatura chimica: Questo metodo coinvolge l’utilizzo di sostanze chimiche che reagiscono con la superficie del metallo, creando uno strato di argento sulla sua superficie. Questa tecnica è spesso impiegata per rivestimenti meno uniformi o in situazioni in cui l’argentatura elettrolitica non è praticabile.
- Argentatura al fuoco: Questo processo prevede l’applicazione di un sottile strato di polvere di argento sulla superficie del metallo, seguito da un trattamento termico che fonde la polvere, formando uno strato uniforme di argento sulla superficie del pezzo. Questa tecnica è particolarmente adatta per metalli ad alta temperatura di fusione.
- Argentatura mediante immersione: Questa tecnica coinvolge l’immersione del pezzo metallico in una soluzione contenente particelle di argento sospese in una soluzione chimica. Le particelle di argento aderiscono alla superficie del metallo per adesione chimica o meccanica.
Cosa si intende per argentatura galvanica ?
L’argentatura galvanica, nota anche come argentatura elettrolitica, è un processo mediante il quale uno strato di argento viene depositato su un metallo di base tramite un’azione elettrochimica controllata. Questo metodo sfrutta i principi dell’elettrolisi, dove un’anodo costituito da argento e un catodo costituito dal metallo da argentare vengono immersi in una soluzione elettrolitica contenente ioni di argento. Quando viene applicata una corrente elettrica, gli ioni di argento si riducono sulla superficie del metallo da argentare, formando uno strato di argento uniforme.
L’argentatura galvanica offre diversi vantaggi, tra cui la capacità di depositare uno strato uniforme di argento su superfici complesse e irregolari, il controllo preciso dello spessore del rivestimento e la resistenza alla corrosione migliorata del metallo di base. Questo processo è ampiamente utilizzato in una vasta gamma di settori industriali per migliorare l’estetica, la conducibilità elettrica e le proprietà anticorrosive dei manufatti metallici.
Cosa si intende per argentatura a freddo?
L’argentatura a freddo è un metodo alternativo per depositare uno strato di argento su una superficie metallica senza utilizzare il calore. A differenza dell’argentatura galvanica, che coinvolge un processo elettrolitico controllato, l’argentatura a freddo si basa su una reazione chimica tra una soluzione contenente ioni di argento e la superficie del metallo da trattare.
Nel processo di argentatura a freddo, la soluzione contenente ioni di argento viene applicata direttamente sulla superficie del metallo mediante immersione, pennellatura o spruzzatura. Gli ioni di argento presenti nella soluzione reagiscono con la superficie del metallo, depositando uno strato sottile di argento. Questo processo è solitamente più lento e meno controllabile rispetto all’argentatura galvanica, ma può essere utilizzato in situazioni in cui l’uso del calore è indesiderato o non praticabile.
L’argentatura a freddo può essere impiegata per scopi decorativi, funzionali o protettivi, a seconda delle esigenze specifiche del manufatto e del processo applicativo. Tuttavia, è importante notare che questo metodo potrebbe non garantire la stessa uniformità e resistenza della argentatura galvanica, soprattutto in termini di spessore e aderenza dello strato di argento.
Cosa si intende per argentatura a spessore?
L’argentatura a spessore si riferisce a un processo di argentatura in cui viene depositato uno strato relativamente più spesso di argento sulla superficie di un oggetto metallico. Questo strato di argento può essere significativamente più spesso rispetto alla normale argentatura elettrolitica o chimica, che solitamente produce uno strato di argento molto sottile.
Nel caso dell’argentatura a spessore, il rivestimento di argento può essere applicato mediante varie tecniche, tra cui l’argentatura galvanica o elettroless, in cui viene utilizzato un processo chimico per depositare lo strato di argento sulla superficie del metallo di base.
L’argentatura a spessore può essere richiesta per una serie di motivi, tra cui:
- Requisiti di resistenza e durabilità: Uno strato più spesso di argento può fornire una maggiore resistenza all’usura e alla corrosione, rendendo il pezzo più durevole nel tempo.
- Proprietà estetiche: Uno strato più spesso di argento può creare un aspetto più brillante e riflettente, migliorando l’estetica del pezzo e conferendogli un valore aggiunto.
- Requisiti funzionali: In alcune applicazioni, uno spessore maggiore di argento può essere necessario per garantire una migliore conducibilità elettrica o termica
Quanto costa fare il bagno d’argento?
Il costo per fare il bagno d’argento dipende da diversi fattori che possono influenzare il costo complessivo del processo. Alcuni dei principali fattori includono:
- Dimensioni e complessità del pezzo: Pezzi più grandi o più complessi possono richiedere più tempo e risorse per essere trattati, influenzando il costo complessivo del bagno d’argento.
- Tipo di metallo di base: Alcuni metalli possono richiedere trattamenti pre-bagno o condizioni speciali per l’argentatura, il che può influenzare i costi.
- Spessore del rivestimento: Il costo può variare a seconda dello spessore di argento richiesto sul pezzo. Maggiore è lo spessore richiesto, maggiore sarà il consumo di materiale argentato e, di conseguenza, maggiore sarà il costo.
- Metodo di argentatura: Tecniche diverse, come l’argentatura galvanica, l’argentatura chimica o altre varianti, possono avere costi di materiale e di lavoro diversi.
- Quantità: Il costo unitario può diminuire all’aumentare della quantità di pezzi da trattare, grazie a economie di scala nel processo di produzione.
- Finitura e specifiche richieste: Se sono richieste finiture speciali o specifiche aggiuntive, come lucidatura, pulizia o controlli di qualità, ciò può influenzare i costi.
- Localizzazione del servizio: Il costo può variare a seconda della regione geografica in cui viene eseguito il bagno d’argento, a causa delle differenze nei costi della manodopera e dei materiali.
- Requisiti ambientali e normative: Se il processo deve essere conforme a determinati standard ambientali o normative, ciò potrebbe comportare costi aggiuntivi per l’implementazione di tecnologie o pratiche specifiche.
Come avviene il processo?
L’ossido che si forma non è dovuto ad un apporto di materiale ma ad una trasformazione della superficie originale dell’oggetto. La superficie di alluminio sottoposta ad anodizzazione viene ossidata progressivamente dall’esterno della superficie progredendo verso l’interno. L’ ossido che si forma ha un volume maggiore del metallo (alluminio) originario per cui apparentemente, dal punto di vista dimensionale, sembra via sia un apporto di materiale, in realtà lo spessore di ossido in parte “penetra” nel metallo in parte “cresce” verso l’esterno. In pratica per uno spessore di es. 10 micron, 5 micron sono penetrati e 5 micron si sono espansi per cui l’aumento geometrico ammonta a 5 micron. Da notare che, su un diametro, lo spessore di 10 micron produce un aumento del diametro pari a 10 micron e non 20.
L’ossido tende a formarsi abbastanza uniformemente anche nei recessi, nei sottosquadra, all’interno di tubi. La struttura dell’ossido è molto simile alla struttura del “nido d’ape” con tubuli verticali rispetto allo spessore formato. Questi tubuli hanno un diametro molto inferiore al micron, ma particolari coloranti vi possono penetrare, potendo conferire allo strato di ossido una grande varietà di colorazioni. Successivamente alla formazione dello strato di ossido e, alla eventuale colorazione, viene eseguita una operazione di chiusura dei pori al fine di garantire compattezza e resistenza alla corrosione. Questa operazione prende il nome di fissaggio e può avvenire a freddo o a caldo. in ogni caso i pori vengono chiusi, risulta tuttavia più sicura l’operazione di fissaggio a caldo soprattutto per gli strati di ossido colorato.
Materiali trattabili
- Acciaio
- Acciaio inox
- Acciaio bonificato
- Ferro
- Rame
- Ottone
- Zama
- Alluminio
- Sinterizzati
Normative
- UNI-ISO 4521
Possibili finiture
- Passivazione bianca (cromo 3)
- Passivazione alta resistenza (cromo 3)
- Passivazione nera (cromo 3)
Dimensioni massime trattabili
900x400x400 mm
Materiali trattabili
- Acciaio
- Acciaio inox
- Acciaio bonificato
- Ferro
- Rame
- Ottone
- Zama
- Alluminio
- Sinterizzati
Possibili finiture
- Passivazione bianca (cromo 3)
- Passivazione alta resistenza (cromo 3)
- Passivazione nera (cromo 3)
Normative
- UNI-ISO 4521
Dimensioni massime trattabili
900x400x400 mm
Settori
d'applicazione
d'applicazione
Settori d'applicazione
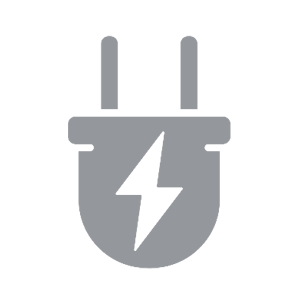
Elettrico
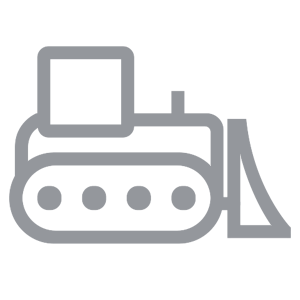
Movimento terra
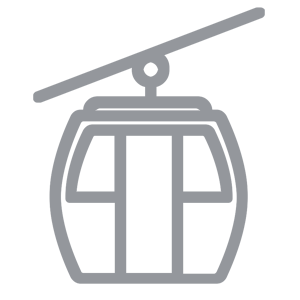
Funivie
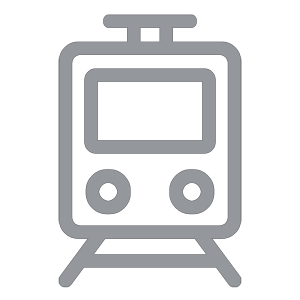
Ferroviario
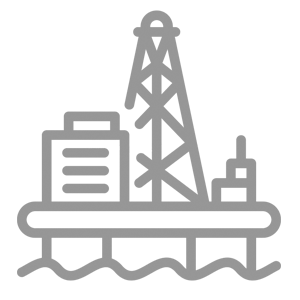
Offshore
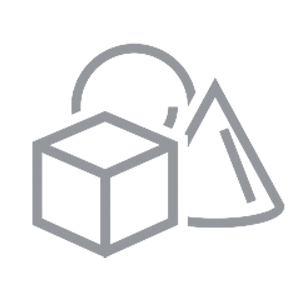
Termotecnico
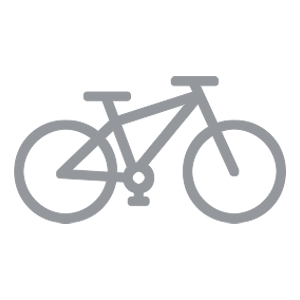
Raccorderia
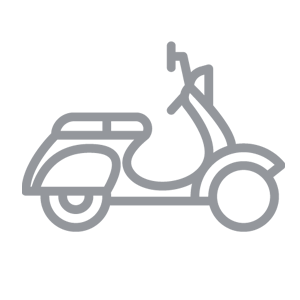