Trattamenti funzionali
Deidrogenazione
Trattamenti funzionali
Deidrogenazione
Trattamenti funzionali: la deidrogenazione
Nel contesto dei trattamenti galvanici,ossia tutti quei processi industriali utilizzati per applicare rivestimenti metallici su materiali, al fine di migliorarne le proprietà superficiali o conferire loro specifiche caratteristiche, la deidrogenazione è un processo cruciale.
A cosa serve la deidrogenazione e perché è importante nei processi galvanici
La deidrogenazione ha il compito di eliminare l’idrogeno assorbito durante i processi galvanici. Se questo idrogeno non viene rimosso, può causare tensioni, microfratture e danni nella struttura cristallina del materiale. Questo processo è cruciale per garantire che gli oggetti trattati mantengano la loro integrità e resistenza nel tempo, soprattutto quando sono sottoposti a sforzi durante l’uso normale.
Come avviene la deidrogenazione
Quando il metallo viene depositato in soluzioni elettrolitiche, si libera anche idrogeno, che può essere assorbito dal materiale base. Questo idrogeno può causare problemi strutturali nel tempo. La deidrogenazione è quindi necessaria per rimuovere efficacemente l’idrogeno assorbito, e questo avviene attraverso un trattamento termico entro un breve periodo dal trattamento galvanico.
Parlando di materiali ferrosi, come l’acciaio, sono particolarmente suscettibili alla deidrogenazione. Questo trattamento termico post-galvanizzazione è vitale per garantire che l’acciaio mantenga la sua resistenza e integrità strutturale nel lungo periodo.
Esplorando la deidrogenazione gli usi pratici
La deidrogenazione, un processo sofisticato, svela il suo potenziale in diverse situazioni. Attraverso l’uso di catalizzatori, questa tecnica avanzata è in grado di rimuovere selettivamente l’idrogeno da molecole specifiche, aprendo nuove strade nella sintesi organica. Scopriamo alcuni dettagli affascinanti dei suoi usi pratici:
● Deidrogenazione dell’Ossidazione: Preservare la robustezza dei materiali
Dopo che i materiali hanno subito il processo di ossidazione, la deidrogenazione diventa vitale. Il suo compito è rimuovere l’idrogeno eventualmente assorbito, evitando la formazione di microfratture e garantendo che la struttura del materiale rimanga intatta nel tempo.
● Deidrogenazione degli Alcani: Versatilità molecolare per nuove prospettive
Nella vastità della sintesi organica, la deidrogenazione degli alcani si presenta come una chiave magica. Questo processo consente di produrre molecole con maggiore insaturazione, offrendo una flessibilità strutturale che apre nuove prospettive di progettazione per composti chimici.
● Deidrogenazione degli Alcoli: Cosa si ottiene per deidrogenazione degli alcoli
Una pratica comune nella sintesi organica, la deidrogenazione degli alcoli è un vero artista della trasformazione. Rimuove atomi di idrogeno dagli alcoli, trasformandoli in composti con maggiore insaturazione come alcheni o chetoni. Questo processo è fondamentale per la creazione di composti chimici specifici, contribuendo così alla diversità e alla specializzazione nella chimica.
● Deidrogenazione Catalitica: Un processo chimico avanzato
La deidrogenazione catalitica è un processo sofisticato che utilizza catalizzatori per rimuovere selettivamente l’idrogeno da molecole specifiche. Questo processo ha ampie applicazioni nella sintesi organica, consentendo reazioni di deidrogenazione controllate e selettive.
Quali sono i vantaggi della deidrogenazione nell’industria galvanica
I vantaggi della deidrogenazione nell’industria galvanica includono la prevenzione di microfratture e danni strutturali causati dall’idrogeno assorbito durante i processi galvanici. Ciò assicura la durabilità e la resistenza degli oggetti trattati, contribuendo alla loro affidabilità nel tempo.
Quali materiali ferrosi sono più suscettibili alla deidrogenazione
In generale, materiali ferrosi come l’acciaio sono più suscettibili alla deidrogenazione. Tuttavia, l’entità della suscettibilità dipende da vari fattori, compresi i dettagli specifici del materiale e del processo di galvanizzazione.
Deidrogenazione in Diversi Contesti: Acciaio, Viti, Nichelatura e Zincatura
● Deidrogenazione dell’Acciaio: Proteggere la resistenza con il trattamento termico
Nel processo galvanico, la deidrogenazione dell’acciaio è fondamentale per prevenire danni strutturali causati dall’idrogeno assorbito durante la deposizione. Dopo la galvanizzazione, un trattamento termico mirato elimina l’idrogeno in eccesso, assicurando la resistenza a fatica del materiale nel tempo.
● Deidrogenazione delle Viti: Garantire la solidità strutturale e la resistenza
Quando si tratta di viti, la deidrogenazione è un passo cruciale. Questo processo essenziale assicura che le viti mantengano la loro integrità strutturale, evitando microfratture che potrebbero compromettere la loro efficacia. Una precauzione necessaria per garantire la robustezza e la durata delle viti.
● Deidrogenazione della Nichelatura: Critica per una superficie forte e durevole
Nel caso della nichelatura, la deidrogenazione è una fase critica. Garantisce la resistenza e l’integrità della superficie nichelata, assicurando che il materiale mantenga qualità e durabilità nel tempo. Un passo indispensabile per preservare la superficie e garantire risultati di alta qualità.
● Deidrogenazione della Zincatura: Proteggere la struttura con un passo chiave
La deidrogenazione nella zincatura è cruciale per rimuovere l’idrogeno assorbito, preservando così la resistenza strutturale dell’oggetto zincato. Questo processo non solo previene microfratture ma protegge anche dall’idrogeno intrappolato. Una precauzione fondamentale per assicurare la robustezza e prevenire danni nel tempo.
Tobaldini e l’impegno per la qualità e la sicurezza
Tobaldini esegue trattamenti di deidrogenazione per garantire la qualità e la sicurezza dei materiali trattati dopo zincatura, cromatura e altri processi. Questo impegno assicura che i materiali trattati mantengano la loro integrità strutturale e resistenza nel tempo.
In conclusione, la deidrogenazione è un passo cruciale nei trattamenti galvanici, contribuendo alla durabilità e all’affidabilità degli oggetti trattati.
Come avviene il processo?
L’ossido che si forma non è dovuto ad un apporto di materiale ma ad una trasformazione della superficie originale dell’oggetto. La superficie di alluminio sottoposta ad anodizzazione viene ossidata progressivamente dall’esterno della superficie progredendo verso l’interno. L’ ossido che si forma ha un volume maggiore del metallo (alluminio) originario per cui apparentemente, dal punto di vista dimensionale, sembra via sia un apporto di materiale, in realtà lo spessore di ossido in parte “penetra” nel metallo in parte “cresce” verso l’esterno. In pratica per uno spessore di es. 10 micron, 5 micron sono penetrati e 5 micron si sono espansi per cui l’aumento geometrico ammonta a 5 micron. Da notare che, su un diametro, lo spessore di 10 micron produce un aumento del diametro pari a 10 micron e non 20.
L’ossido tende a formarsi abbastanza uniformemente anche nei recessi, nei sottosquadra, all’interno di tubi. La struttura dell’ossido è molto simile alla struttura del “nido d’ape” con tubuli verticali rispetto allo spessore formato. Questi tubuli hanno un diametro molto inferiore al micron, ma particolari coloranti vi possono penetrare, potendo conferire allo strato di ossido una grande varietà di colorazioni. Successivamente alla formazione dello strato di ossido e, alla eventuale colorazione, viene eseguita una operazione di chiusura dei pori al fine di garantire compattezza e resistenza alla corrosione. Questa operazione prende il nome di fissaggio e può avvenire a freddo o a caldo. in ogni caso i pori vengono chiusi, risulta tuttavia più sicura l’operazione di fissaggio a caldo soprattutto per gli strati di ossido colorato.
Trattamenti funzionali: la deidrogenazione
Nel contesto dei trattamenti galvanici,ossia tutti quei processi industriali utilizzati per applicare rivestimenti metallici su materiali, al fine di migliorarne le proprietà superficiali o conferire loro specifiche caratteristiche, la deidrogenazione è un processo cruciale.
A cosa serve la deidrogenazione e perché è importante nei processi galvanici
La deidrogenazione ha il compito di eliminare l’idrogeno assorbito durante i processi galvanici. Se questo idrogeno non viene rimosso, può causare tensioni, microfratture e danni nella struttura cristallina del materiale. Questo processo è cruciale per garantire che gli oggetti trattati mantengano la loro integrità e resistenza nel tempo, soprattutto quando sono sottoposti a sforzi durante l’uso normale.
Come avviene la deidrogenazione
Quando il metallo viene depositato in soluzioni elettrolitiche, si libera anche idrogeno, che può essere assorbito dal materiale base. Questo idrogeno può causare problemi strutturali nel tempo. La deidrogenazione è quindi necessaria per rimuovere efficacemente l’idrogeno assorbito, e questo avviene attraverso un trattamento termico entro un breve periodo dal trattamento galvanico.
Parlando di materiali ferrosi, come l’acciaio, sono particolarmente suscettibili alla deidrogenazione. Questo trattamento termico post-galvanizzazione è vitale per garantire che l’acciaio mantenga la sua resistenza e integrità strutturale nel lungo periodo.
Esplorando la deidrogenazione gli usi pratici
La deidrogenazione, un processo sofisticato, svela il suo potenziale in diverse situazioni. Attraverso l’uso di catalizzatori, questa tecnica avanzata è in grado di rimuovere selettivamente l’idrogeno da molecole specifiche, aprendo nuove strade nella sintesi organica. Scopriamo alcuni dettagli affascinanti dei suoi usi pratici:
● Deidrogenazione dell’Ossidazione: Preservare la robustezza dei materiali
Dopo che i materiali hanno subito il processo di ossidazione, la deidrogenazione diventa vitale. Il suo compito è rimuovere l’idrogeno eventualmente assorbito, evitando la formazione di microfratture e garantendo che la struttura del materiale rimanga intatta nel tempo.
● Deidrogenazione degli Alcani: Versatilità molecolare per nuove prospettive
Nella vastità della sintesi organica, la deidrogenazione degli alcani si presenta come una chiave magica. Questo processo consente di produrre molecole con maggiore insaturazione, offrendo una flessibilità strutturale che apre nuove prospettive di progettazione per composti chimici.
● Deidrogenazione degli Alcoli: Cosa si ottiene per deidrogenazione degli alcoli
Una pratica comune nella sintesi organica, la deidrogenazione degli alcoli è un vero artista della trasformazione. Rimuove atomi di idrogeno dagli alcoli, trasformandoli in composti con maggiore insaturazione come alcheni o chetoni. Questo processo è fondamentale per la creazione di composti chimici specifici, contribuendo così alla diversità e alla specializzazione nella chimica.
● Deidrogenazione Catalitica: Un processo chimico avanzato
La deidrogenazione catalitica è un processo sofisticato che utilizza catalizzatori per rimuovere selettivamente l’idrogeno da molecole specifiche. Questo processo ha ampie applicazioni nella sintesi organica, consentendo reazioni di deidrogenazione controllate e selettive.
Quali sono i vantaggi della deidrogenazione nell’industria galvanica
I vantaggi della deidrogenazione nell’industria galvanica includono la prevenzione di microfratture e danni strutturali causati dall’idrogeno assorbito durante i processi galvanici. Ciò assicura la durabilità e la resistenza degli oggetti trattati, contribuendo alla loro affidabilità nel tempo.
Quali materiali ferrosi sono più suscettibili alla deidrogenazione
In generale, materiali ferrosi come l’acciaio sono più suscettibili alla deidrogenazione. Tuttavia, l’entità della suscettibilità dipende da vari fattori, compresi i dettagli specifici del materiale e del processo di galvanizzazione.
Deidrogenazione in Diversi Contesti: Acciaio, Viti, Nichelatura e Zincatura
● Deidrogenazione dell’Acciaio: Proteggere la resistenza con il trattamento termico
Nel processo galvanico, la deidrogenazione dell’acciaio è fondamentale per prevenire danni strutturali causati dall’idrogeno assorbito durante la deposizione. Dopo la galvanizzazione, un trattamento termico mirato elimina l’idrogeno in eccesso, assicurando la resistenza a fatica del materiale nel tempo.
● Deidrogenazione delle Viti: Garantire la solidità strutturale e la resistenza
Quando si tratta di viti, la deidrogenazione è un passo cruciale. Questo processo essenziale assicura che le viti mantengano la loro integrità strutturale, evitando microfratture che potrebbero compromettere la loro efficacia. Una precauzione necessaria per garantire la robustezza e la durata delle viti.
● Deidrogenazione della Nichelatura: Critica per una superficie forte e durevole
Nel caso della nichelatura, la deidrogenazione è una fase critica. Garantisce la resistenza e l’integrità della superficie nichelata, assicurando che il materiale mantenga qualità e durabilità nel tempo. Un passo indispensabile per preservare la superficie e garantire risultati di alta qualità.
● Deidrogenazione della Zincatura: Proteggere la struttura con un passo chiave
La deidrogenazione nella zincatura è cruciale per rimuovere l’idrogeno assorbito, preservando così la resistenza strutturale dell’oggetto zincato. Questo processo non solo previene microfratture ma protegge anche dall’idrogeno intrappolato. Una precauzione fondamentale per assicurare la robustezza e prevenire danni nel tempo.
Tobaldini e l’impegno per la qualità e la sicurezza
Tobaldini esegue trattamenti di deidrogenazione per garantire la qualità e la sicurezza dei materiali trattati dopo zincatura, cromatura e altri processi. Questo impegno assicura che i materiali trattati mantengano la loro integrità strutturale e resistenza nel tempo.
In conclusione, la deidrogenazione è un passo cruciale nei trattamenti galvanici, contribuendo alla durabilità e all’affidabilità degli oggetti trattati.
Come avviene il processo?
L’ossido che si forma non è dovuto ad un apporto di materiale ma ad una trasformazione della superficie originale dell’oggetto. La superficie di alluminio sottoposta ad anodizzazione viene ossidata progressivamente dall’esterno della superficie progredendo verso l’interno. L’ ossido che si forma ha un volume maggiore del metallo (alluminio) originario per cui apparentemente, dal punto di vista dimensionale, sembra via sia un apporto di materiale, in realtà lo spessore di ossido in parte “penetra” nel metallo in parte “cresce” verso l’esterno. In pratica per uno spessore di es. 10 micron, 5 micron sono penetrati e 5 micron si sono espansi per cui l’aumento geometrico ammonta a 5 micron. Da notare che, su un diametro, lo spessore di 10 micron produce un aumento del diametro pari a 10 micron e non 20.
L’ossido tende a formarsi abbastanza uniformemente anche nei recessi, nei sottosquadra, all’interno di tubi. La struttura dell’ossido è molto simile alla struttura del “nido d’ape” con tubuli verticali rispetto allo spessore formato. Questi tubuli hanno un diametro molto inferiore al micron, ma particolari coloranti vi possono penetrare, potendo conferire allo strato di ossido una grande varietà di colorazioni. Successivamente alla formazione dello strato di ossido e, alla eventuale colorazione, viene eseguita una operazione di chiusura dei pori al fine di garantire compattezza e resistenza alla corrosione. Questa operazione prende il nome di fissaggio e può avvenire a freddo o a caldo. in ogni caso i pori vengono chiusi, risulta tuttavia più sicura l’operazione di fissaggio a caldo soprattutto per gli strati di ossido colorato.
Materiali trattabili
- Acciaio al carbonio
- Ferro
- Acciaio inox
- Rame
- Ottone
- Alluminio
Normative
- UNI ISO 6158
- UNI 5082
Possibili finiture
- Passivazione bianca (cromo 3)
- Passivazione alta resistenza (cromo 3)
- Passivazione nera (cromo 3)
Dimensioni massime trattabili
2700x500x1200 mm
Materiali trattabili
- Acciaio al carbonio
- Ferro
- Acciaio inox
- Rame
- Ottone
- Alluminio
Possibili finiture
- Passivazione bianca (cromo 3)
- Passivazione alta resistenza (cromo 3)
- Passivazione nera (cromo 3)
Normative
- UNI ISO 6158
- UNI 5082
Dimensioni massime trattabili
2700x500x1200 mm
Settori
d'applicazione
d'applicazione
Settori d'applicazione
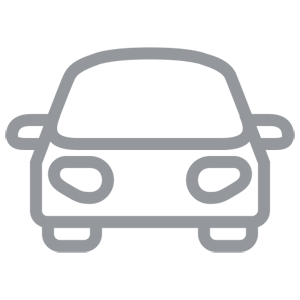
Automotive
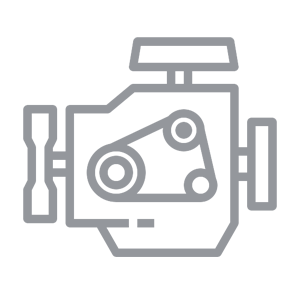
Meccanica
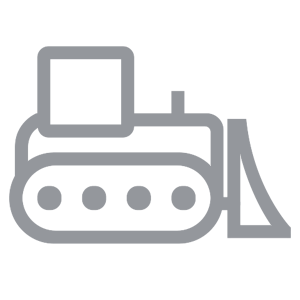
Movimento terra
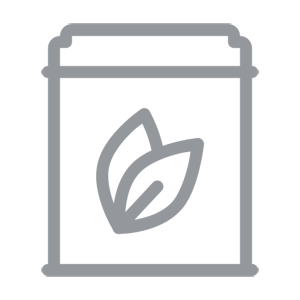