Trattamenti decorativi
RAMATURA
Trattamenti decorativi
Ramatura
Potenziare la Durabilità e l'Affidabilità: Il Ruolo Cruciale della Ramatura dei Metalli
La ramatura dei metalli è un processo di trattamento superficiale che viene utilizzato per migliorare le proprietà meccaniche, chimiche e fisiche dei metalli. Questo processo coinvolge l’applicazione di uno strato protettivo di metallo su una superficie di un metallo base attraverso varie tecniche, come galvanizzazione, elettrodeposizione, sputtering o deposizione chimica da vapore. L’obiettivo principale della ramatura è quello di fornire protezione contro la corrosione, l’usura, l’abrasione e altri danni ambientali, migliorando così la durabilità e l’affidabilità del metallo trattato. Inoltre, la ramatura può essere utilizzata anche per scopi estetici, conferendo al metallo una finitura più attraente e luminosa. Questo processo è ampiamente utilizzato in una vasta gamma di settori, tra cui l’automotive, l’aerospaziale, l’elettronica, la costruzione e molti altri, dove la resistenza e l’aspetto del metallo sono critici per le prestazioni e l’estetica del prodotto finale.
A cosa serve
la ramatura?
La ramatura dei metalli serve a diversi scopi:
- Protezione dalla corrosione: Uno degli utilizzi principali della ramatura è quello di proteggere i metalli dalla corrosione atmosferica, chimica o elettrochimica. Lo strato protettivo applicato durante il processo di ramatura funge da barriera tra il metallo base e l’ambiente circostante, prevenendo così la formazione di ruggine o altri danni corrosivi.
- Resistenza all’usura e all’abrasione: La ramatura può migliorare la resistenza del metallo trattato all’usura e all’abrasione, prolungandone così la durata e la vita utile. Questo è particolarmente importante in applicazioni in cui il metallo è soggetto a sollecitazioni meccaniche o a contatto con materiali abrasivi.
- Miglioramento delle proprietà superficiali: La ramatura può migliorare le proprietà superficiali del metallo, come la durezza, la resistenza alla trazione, la resistenza alla fatica e la resistenza alle sollecitazioni termiche, rendendolo più adatto per specifiche applicazioni o ambienti operativi.
- Miglioramento estetico: In molti casi, la ramatura viene utilizzata anche per migliorare l’aspetto estetico del metallo, conferendogli una finitura più brillante, uniforme o decorativa. Questo è particolarmente importante in settori come l’automotive, l’arredamento e l’industria dell’alta moda, dove l’aspetto estetico del metallo è cruciale per l’attrattiva del prodotto finale.
In sintesi, la ramatura dei metalli è un processo versatile che offre una serie di vantaggi, tra cui protezione dalla corrosione, resistenza all’usura, miglioramento delle proprietà superficiali e miglioramento estetico, contribuendo così a migliorare le prestazioni e l’affidabilità dei prodotti metallici in una vasta gamma di applicazioni industriali e commerciali.
La ramatura elettrolitica
La ramatura elettrolitica è un processo di trattamento superficiale dei metalli che coinvolge l’immersione di un oggetto metallico in una soluzione elettrolitica contenente ioni metallici. Durante questo processo, viene applicata una differenza di potenziale tra l’oggetto da trattare, chiamato catodo, e un anodo composto da un metallo di sacrificio o da un materiale conduttivo appropriato. L’applicazione di corrente elettrica induce la migrazione degli ioni metallici dalla soluzione elettrolitica verso la superficie del catodo, dove si depositano formando uno strato metallico protettivo.
Questo strato metallico può avere diverse proprietà a seconda delle condizioni del processo, tra cui spessore, durezza, aderenza e composizione chimica. La ramatura elettrolitica può essere utilizzata per una varietà di scopi, tra cui protezione dalla corrosione, miglioramento delle proprietà meccaniche e estetiche del metallo, e preparazione della superficie per ulteriori trattamenti o rivestimenti. È un processo ampiamente utilizzato nell’industria manifatturiera per migliorare le prestazioni e l’affidabilità dei componenti metallici in una vasta gamma di applicazioni.
Come avviene il processo?
L’ossido che si forma non è dovuto ad un apporto di materiale ma ad una trasformazione della superficie originale dell’oggetto. La superficie di alluminio sottoposta ad anodizzazione viene ossidata progressivamente dall’esterno della superficie progredendo verso l’interno. L’ ossido che si forma ha un volume maggiore del metallo (alluminio) originario per cui apparentemente, dal punto di vista dimensionale, sembra via sia un apporto di materiale, in realtà lo spessore di ossido in parte “penetra” nel metallo in parte “cresce” verso l’esterno. In pratica per uno spessore di es. 10 micron, 5 micron sono penetrati e 5 micron si sono espansi per cui l’aumento geometrico ammonta a 5 micron. Da notare che, su un diametro, lo spessore di 10 micron produce un aumento del diametro pari a 10 micron e non 20.
L’ossido tende a formarsi abbastanza uniformemente anche nei recessi, nei sottosquadra, all’interno di tubi. La struttura dell’ossido è molto simile alla struttura del “nido d’ape” con tubuli verticali rispetto allo spessore formato. Questi tubuli hanno un diametro molto inferiore al micron, ma particolari coloranti vi possono penetrare, potendo conferire allo strato di ossido una grande varietà di colorazioni. Successivamente alla formazione dello strato di ossido e, alla eventuale colorazione, viene eseguita una operazione di chiusura dei pori al fine di garantire compattezza e resistenza alla corrosione. Questa operazione prende il nome di fissaggio e può avvenire a freddo o a caldo. in ogni caso i pori vengono chiusi, risulta tuttavia più sicura l’operazione di fissaggio a caldo soprattutto per gli strati di ossido colorato.
Potenziare la Durabilità e l'Affidabilità: Il Ruolo Cruciale della Ramatura dei Metalli
La ramatura dei metalli è un processo di trattamento superficiale che viene utilizzato per migliorare le proprietà meccaniche, chimiche e fisiche dei metalli. Questo processo coinvolge l’applicazione di uno strato protettivo di metallo su una superficie di un metallo base attraverso varie tecniche, come galvanizzazione, elettrodeposizione, sputtering o deposizione chimica da vapore. L’obiettivo principale della ramatura è quello di fornire protezione contro la corrosione, l’usura, l’abrasione e altri danni ambientali, migliorando così la durabilità e l’affidabilità del metallo trattato. Inoltre, la ramatura può essere utilizzata anche per scopi estetici, conferendo al metallo una finitura più attraente e luminosa. Questo processo è ampiamente utilizzato in una vasta gamma di settori, tra cui l’automotive, l’aerospaziale, l’elettronica, la costruzione e molti altri, dove la resistenza e l’aspetto del metallo sono critici per le prestazioni e l’estetica del prodotto finale.
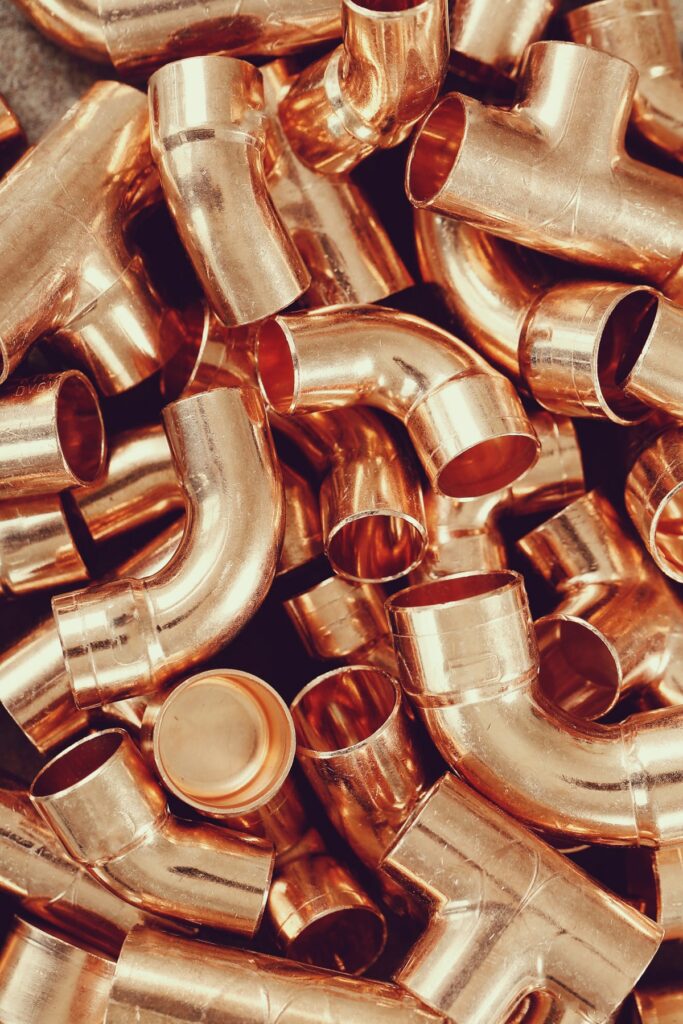
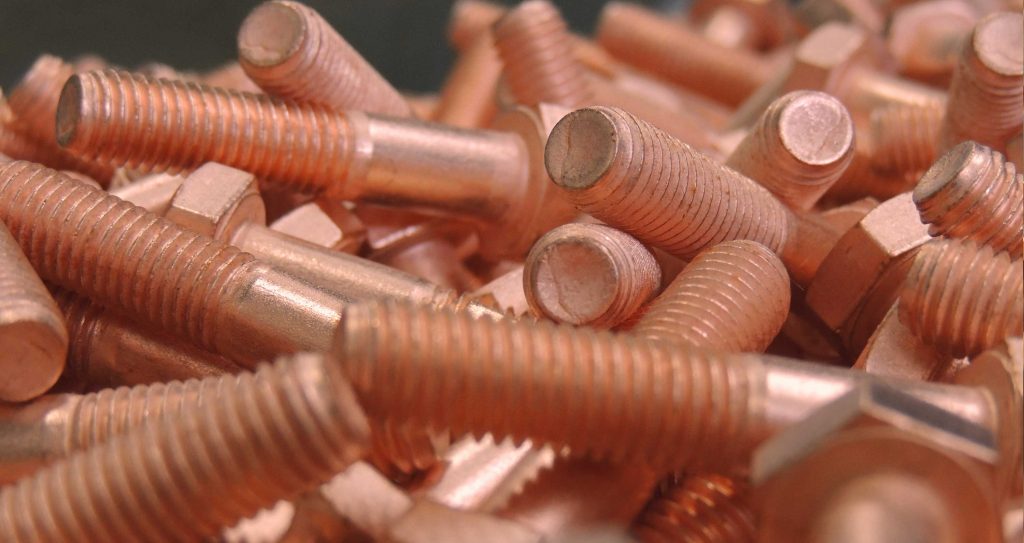
A Cosa Serve la Ramatura
A cosa serve la ramatura?
La ramatura dei metalli serve a diversi scopi:
- Protezione dalla corrosione: Uno degli utilizzi principali della ramatura è quello di proteggere i metalli dalla corrosione atmosferica, chimica o elettrochimica. Lo strato protettivo applicato durante il processo di ramatura funge da barriera tra il metallo base e l’ambiente circostante, prevenendo così la formazione di ruggine o altri danni corrosivi.
- Resistenza all’usura e all’abrasione: La ramatura può migliorare la resistenza del metallo trattato all’usura e all’abrasione, prolungandone così la durata e la vita utile. Questo è particolarmente importante in applicazioni in cui il metallo è soggetto a sollecitazioni meccaniche o a contatto con materiali abrasivi.
- Miglioramento delle proprietà superficiali: La ramatura può migliorare le proprietà superficiali del metallo, come la durezza, la resistenza alla trazione, la resistenza alla fatica e la resistenza alle sollecitazioni termiche, rendendolo più adatto per specifiche applicazioni o ambienti operativi.
- Miglioramento estetico: In molti casi, la ramatura viene utilizzata anche per migliorare l’aspetto estetico del metallo, conferendogli una finitura più brillante, uniforme o decorativa. Questo è particolarmente importante in settori come l’automotive, l’arredamento e l’industria dell’alta moda, dove l’aspetto estetico del metallo è cruciale per l’attrattiva del prodotto finale.
In sintesi, la ramatura dei metalli è un processo versatile che offre una serie di vantaggi, tra cui protezione dalla corrosione, resistenza all’usura, miglioramento delle proprietà superficiali e miglioramento estetico, contribuendo così a migliorare le prestazioni e l’affidabilità dei prodotti metallici in una vasta gamma di applicazioni industriali e commerciali.
CONTATTACI!
La ramatura elettrolitica
La ramatura elettrolitica è un processo di trattamento superficiale dei metalli che coinvolge l’immersione di un oggetto metallico in una soluzione elettrolitica contenente ioni metallici. Durante questo processo, viene applicata una differenza di potenziale tra l’oggetto da trattare, chiamato catodo, e un anodo composto da un metallo di sacrificio o da un materiale conduttivo appropriato. L’applicazione di corrente elettrica induce la migrazione degli ioni metallici dalla soluzione elettrolitica verso la superficie del catodo, dove si depositano formando uno strato metallico protettivo.
Questo strato metallico può avere diverse proprietà a seconda delle condizioni del processo, tra cui spessore, durezza, aderenza e composizione chimica. La ramatura elettrolitica può essere utilizzata per una varietà di scopi, tra cui protezione dalla corrosione, miglioramento delle proprietà meccaniche e estetiche del metallo, e preparazione della superficie per ulteriori trattamenti o rivestimenti. È un processo ampiamente utilizzato nell’industria manifatturiera per migliorare le prestazioni e l’affidabilità dei componenti metallici in una vasta gamma di applicazioni.
Come avviene il processo?
L’ossido che si forma non è dovuto ad un apporto di materiale ma ad una trasformazione della superficie originale dell’oggetto. La superficie di alluminio sottoposta ad anodizzazione viene ossidata progressivamente dall’esterno della superficie progredendo verso l’interno. L’ ossido che si forma ha un volume maggiore del metallo (alluminio) originario per cui apparentemente, dal punto di vista dimensionale, sembra via sia un apporto di materiale, in realtà lo spessore di ossido in parte “penetra” nel metallo in parte “cresce” verso l’esterno. In pratica per uno spessore di es. 10 micron, 5 micron sono penetrati e 5 micron si sono espansi per cui l’aumento geometrico ammonta a 5 micron. Da notare che, su un diametro, lo spessore di 10 micron produce un aumento del diametro pari a 10 micron e non 20.
L’ossido tende a formarsi abbastanza uniformemente anche nei recessi, nei sottosquadra, all’interno di tubi. La struttura dell’ossido è molto simile alla struttura del “nido d’ape” con tubuli verticali rispetto allo spessore formato. Questi tubuli hanno un diametro molto inferiore al micron, ma particolari coloranti vi possono penetrare, potendo conferire allo strato di ossido una grande varietà di colorazioni. Successivamente alla formazione dello strato di ossido e, alla eventuale colorazione, viene eseguita una operazione di chiusura dei pori al fine di garantire compattezza e resistenza alla corrosione. Questa operazione prende il nome di fissaggio e può avvenire a freddo o a caldo. in ogni caso i pori vengono chiusi, risulta tuttavia più sicura l’operazione di fissaggio a caldo soprattutto per gli strati di ossido colorato.
La Ramatura Chimica
La ramatura chimica è un processo di trattamento superficiale dei metalli che avviene attraverso l’immersione dell’oggetto metallico in una soluzione chimica specificamente formulata. Durante questo processo, la superficie del metallo reagisce con gli agenti chimici presenti nella soluzione, formando uno strato protettivo sulla superficie dell’oggetto.
Questa reazione chimica può comportare la formazione di composti che migliorano le proprietà del metallo, come la resistenza alla corrosione, all’usura o alle alte temperature. La composizione e le condizioni della soluzione chimica vengono attentamente controllate per ottenere gli effetti desiderati e garantire un trattamento uniforme sulla superficie del metallo.
La ramatura chimica è utilizzata in diversi settori industriali per migliorare le prestazioni e l’affidabilità dei componenti metallici, ed è particolarmente adatta per oggetti con forme complesse o per materiali sensibili alla temperatura o alla corrosione. È un processo efficace e conveniente per ottenere una protezione superficiale uniforme e duratura sui metalli.
La ramatura chimica è un processo di trattamento superficiale dei metalli che avviene attraverso l’immersione dell’oggetto metallico in una soluzione chimica specificamente formulata. Durante questo processo, la superficie del metallo reagisce con gli agenti chimici presenti nella soluzione, formando uno strato protettivo sulla superficie dell’oggetto.
Questa reazione chimica può comportare la formazione di composti che migliorano le proprietà del metallo, come la resistenza alla corrosione, all’usura o alle alte temperature. La composizione e le condizioni della soluzione chimica vengono attentamente controllate per ottenere gli effetti desiderati e garantire un trattamento uniforme sulla superficie del metallo.
La ramatura chimica è utilizzata in diversi settori industriali per migliorare le prestazioni e l’affidabilità dei componenti metallici, ed è particolarmente adatta per oggetti con forme complesse o per materiali sensibili alla temperatura o alla corrosione. È un processo efficace e conveniente per ottenere una protezione superficiale uniforme e duratura sui metalli.
La Ramatura Alcalina
La ramatura alcalina è un processo di trattamento superficiale dei metalli che coinvolge l’immersione dell’oggetto metallico in una soluzione alcalina contenente sostanze chimiche come idrossidi di sodio o potassio. Durante questo processo, la soluzione alcalina reagisce con la superficie del metallo, formando uno strato protettivo di ossidi metallici o idrossidi sul suo substrato.
Questa reazione chimica modifica la superficie del metallo, conferendogli proprietà migliorate come la resistenza alla corrosione e l’aderenza dei rivestimenti successivi. La ramatura alcalina è particolarmente efficace per la pulizia e la preparazione delle superfici metalliche prima di applicare rivestimenti protettivi o decorativi.
Uno dei vantaggi principali della ramatura alcalina è la sua capacità di rimuovere efficacemente oli, grassi, residui di lavorazione e altri contaminanti dalla superficie del metallo, migliorando così l’adesione dei rivestimenti successivi e assicurando una protezione più duratura.
La ramatura alcalina è ampiamente utilizzata in settori come l’industria automobilistica, l’aerospaziale, l’elettronica e la produzione di apparecchiature industriali, dove la protezione dei metalli contro la corrosione e l’usura è fondamentale per la durata e le prestazioni dei prodotti finali.
La ramatura alcalina è un processo di trattamento superficiale dei metalli che coinvolge l’immersione dell’oggetto metallico in una soluzione alcalina contenente sostanze chimiche come idrossidi di sodio o potassio. Durante questo processo, la soluzione alcalina reagisce con la superficie del metallo, formando uno strato protettivo di ossidi metallici o idrossidi sul suo substrato.
Questa reazione chimica modifica la superficie del metallo, conferendogli proprietà migliorate come la resistenza alla corrosione e l’aderenza dei rivestimenti successivi. La ramatura alcalina è particolarmente efficace per la pulizia e la preparazione delle superfici metalliche prima di applicare rivestimenti protettivi o decorativi.
Uno dei vantaggi principali della ramatura alcalina è la sua capacità di rimuovere efficacemente oli, grassi, residui di lavorazione e altri contaminanti dalla superficie del metallo, migliorando così l’adesione dei rivestimenti successivi e assicurando una protezione più duratura.
La ramatura alcalina è ampiamente utilizzata in settori come l’industria automobilistica, l’aerospaziale, l’elettronica e la produzione di apparecchiature industriali, dove la protezione dei metalli contro la corrosione e l’usura è fondamentale per la durata e le prestazioni dei prodotti finali.
La ramatura del Ferro
La ramatura del ferro è un processo di trattamento superficiale finalizzato a proteggere il ferro dalla corrosione e dall’usura. Questo metodo prevede l’applicazione di uno strato protettivo sulla superficie del ferro attraverso tecniche come la galvanizzazione, la verniciatura o la ramatura chimica.
Uno dei metodi più comuni per la ramatura del ferro è la galvanizzazione, che comporta l’immersione del ferro in una soluzione di zinco fuso o in una soluzione elettrolitica contenente ioni di zinco. Durante il processo, gli ioni di zinco si depositano sulla superficie del ferro, formando uno strato di zinco metallico che protegge il ferro dalla corrosione. Questo strato di zinco fornisce una barriera fisica tra il ferro e l’ambiente circostante, prevenendo la formazione di ruggine e prolungando la durata utile del materiale.
Altre tecniche di ramatura del ferro includono la verniciatura con primer zincato o l’applicazione di rivestimenti protettivi a base di resine epossidiche o poliuretaniche. Questi rivestimenti forniscono una protezione aggiuntiva contro la corrosione e l’usura, proteggendo il ferro anche in ambienti aggressivi o esposti agli agenti atmosferici.
In sintesi, la ramatura del ferro è un processo essenziale per garantire la durabilità e la resistenza del materiale, proteggendolo dalla corrosione e dall’usura e prolungandone la vita utile in una varietà di applicazioni industriali e commerciali.
Hai bisogno di aiuto?
Cos'è la Ramatura a Spessore
La ramatura a spessore è un processo di trattamento superficiale dei metalli che comporta l’applicazione di uno strato significativo di materiale protettivo sulla superficie del metallo. A differenza di altri metodi di ramatura che creano uno strato sottile e uniforme, la ramatura a spessore si caratterizza per la deposizione di uno strato più spesso di materiale protettivo.
Questo processo viene solitamente utilizzato quando è necessaria una protezione più robusta contro la corrosione, l’usura o altri danni ambientali. La ramatura a spessore può essere ottenuta attraverso vari metodi, tra cui la galvanizzazione a immersione a caldo, dove il metallo base viene completamente immerso in un bagno di metallo fuso, come lo zinco o l’alluminio, formando uno strato spesso e uniforme sulla sua superficie.
Altri metodi per ottenere la ramatura a spessore includono la deposizione chimica da vapore (CVD) e la deposizione fisica da vapore (PVD), che permettono di applicare uno strato spesso di materiale protettivo utilizzando processi di deposizione sotto vuoto.
La ramatura a spessore viene comunemente impiegata in settori quali la produzione di componenti meccanici, l’industria navale, la costruzione di infrastrutture e altre applicazioni dove è richiesta una protezione resistente e duratura contro l’ambiente aggressivo.
La ramatura dei metalli rappresenta un processo essenziale e versatile nell’ambito della lavorazione dei materiali metallici. Attraverso l’applicazione di strati protettivi sulla superficie dei metalli, la ramatura offre una serie di vantaggi significativi, tra cui la protezione dalla corrosione, l’incremento della resistenza meccanica, la migliorata durabilità e l’estetica.
Sia che si tratti di ramatura elettrolitica, chimica, alcalina o altri metodi, ciascuna tecnica ha il suo ruolo specifico e le sue applicazioni preferenziali, consentendo di adattare il trattamento alle esigenze specifiche del materiale e dell’applicazione finale.
In un mondo in cui l’affidabilità e la longevità dei prodotti sono sempre più cruciali, la ramatura dei metalli si conferma come un’importante risorsa per garantire la qualità e le prestazioni dei componenti metallici in una vasta gamma di settori industriali. La continua ricerca e sviluppo nel campo della ramatura dei metalli promettono di migliorare ulteriormente questa tecnologia, consentendo di soddisfare le esigenze emergenti e di anticipare le sfide future nel settore della lavorazione dei metalli.
hai bisogni di aiuto?
Materiali trattabili
- Acciaio al carbonio
- Ferro
- Acciaio inox
- Rame
- Ottone
- Alluminio
Normative
- UNI ISO 6158
- UNI 5082
Possibili finiture
- Passivazione bianca (cromo 3)
- Passivazione alta resistenza (cromo 3)
- Passivazione nera (cromo 3)
Dimensioni massime trattabili
2700x500x1200 mm
Materiali trattabili
- Ferro
- Rame
- Ottone
- Alluminio
Possibili finiture
- Passivazione bianca (cromo 3)
- Passivazione alta resistenza (cromo 3)
- Passivazione nera (cromo 3)
Normative
- UNI ISO 6158
- UNI 5082
Dimensioni massime trattabili
2700x500x1200 mm
Settori
d'applicazione
d'applicazione
Settori d'applicazione
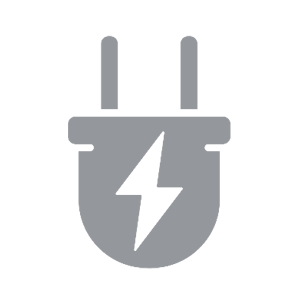
Elettrotecnico
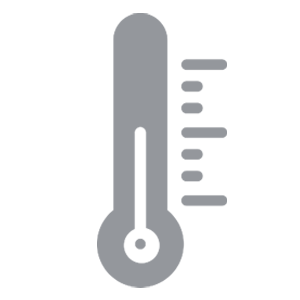
Termotecnico
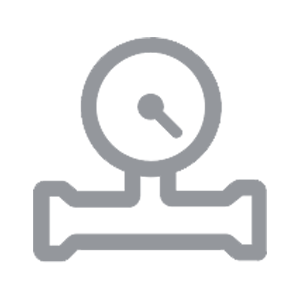
Raccorderia
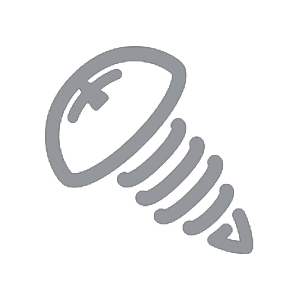