Decorative treatments
Brassing
Decorative treatments
Brassing
Decorative treatments: brass plating
If you are a metal enthusiast and like the brass-plated effect, brass-plating is definitely the solution for you.
In this article we are going to inform you about the various plating techniques to achieve the brass-plated effect on different types of metals, and we are also going to analyze the differences between brass plating and galvanic gold plating, which is also highly sought after.
What is brassing?
Brass plating refers to a matte finish that coats metals giving them that classic golden yellow color of brass.
This process is done mainly to protect the metal from corrosion and make it better resistant to wear and tear, but also for aesthetic reasons, such as to recreate an old-time, vintage effect on iron or stainless steel objects. However, brass plating should not be confused with galvanic gold plating, as these are two totally different processes with equally different aesthetic results.
How to do the brassing?
Brass plating is a process of coating metals by applying a very thin layer of copper to the surface that is to be brassed. An oxidation treatment is then applied to give the object that matte finish.
Brassing metals
For each metal you want to brass-plate, there is a different brass-plating technique.
For example, for iron brass-plating, one proceeds by immersing the object to be treated in a solution composed of copper salts and hydrochloric acid to impart that old gold color.
Brassing can also be done on copper, brass itself, and steel.
In this case, however, it is necessary to go to use a solution that is obtained by diluting hydrochloric acid and nitric acid.
Whatever the technique to be applied and the metal to be treated, it is of paramount importance to go in and clean the surface of the object very thoroughly before brass-plating to ensure that the finish comes out evenly and without imperfections.
Galvanic gilding, differences with brass plating
The major difference between brass plating and electroplated gilding lies in the material that is used to finish the object.
In the case of brass plating, copper is used while gold or silver is used for galvanic gilding.
Certainly galvanic gilding provides a better aesthetic result, more luxury, and greater wear resistance than brass-plated objects that can easily oxidize, but the price is much higher than brass-plating and the process is much longer.
With brass plating, on the other hand, an inexpensive result can be achieved, which is precisely why it is often chosen especially when applied to everyday objects. If, on the other hand, we are dealing with valuable objects then opting for electroplated gilding is definitely the best choice.
How does the process take place?
The oxide that is formed is not due to material input but to a transformation of the original surface of the object. The aluminum surface undergoing anodizing is progressively oxidized from the outside of the surface progressing inward. The ‘oxide that is formed has a larger volume than the original metal (aluminum) so that apparently, from a dimensional point of view, it seems away is a material contribution, in reality the thickness of oxide partly “penetrates” into the metal partly “grows” outward. In practice for a thickness of e.g. 10 microns, 5 microns penetrated and 5 microns expanded so the geometric increase amounts to 5 microns. Note that, on a diameter, the 10-micron thickness produces an increase in diameter of 10 microns, not 20.
Oxide also tends to form fairly uniformly in recesses, undercuts, and inside pipes. The structure of the oxide is very similar to the “honeycomb” structure with vertical tubules with respect to the thickness formed. These tubules are much less than a micron in diameter, but particular dyes can penetrate them, being able to impart a wide variety of colorations to the oxide layer. Following the formation of the oxide layer and, eventual staining, a pore-closing operation is performed in order to ensure compactness and corrosion resistance. This operation is called fixing and can be done cold or hot. in any case, the pores are closed; however, it turns out to be safer to heat fix especially for colored oxide layers.
Decorative treatments: brass plating
If you are a metal enthusiast and like the brass-plated effect, brass-plating is definitely the solution for you.
In this article we are going to inform you about the various plating techniques to achieve the brass-plated effect on different types of metals, and we are also going to analyze the differences between brass plating and galvanic gold plating, which is also highly sought after.
What is brassing?
Brass plating refers to a matte finish that coats metals giving them that classic golden yellow color of brass.
This process is done mainly to protect the metal from corrosion and make it better resistant to wear and tear, but also for aesthetic reasons, such as to recreate an old-time, vintage effect on iron or stainless steel objects. However, brass plating should not be confused with galvanic gold plating, as these are two totally different processes with equally different aesthetic results.
How to do the brassing?
Brass plating is a process of coating metals by applying a very thin layer of copper to the surface that is to be brassed. An oxidation treatment is then applied to give the object that matte finish.
Brassing metals
For each metal you want to brass-plate, there is a different brass-plating technique.
For example, for iron brass-plating, one proceeds by immersing the object to be treated in a solution composed of copper salts and hydrochloric acid to impart that old gold color.
Brassing can also be done on copper, brass itself, and steel.
In this case, however, it is necessary to go to use a solution that is obtained by diluting hydrochloric acid and nitric acid.
Whatever the technique to be applied and the metal to be treated, it is of paramount importance to go in and clean the surface of the object very thoroughly before brass-plating to ensure that the finish comes out evenly and without imperfections.
Galvanic gilding, differences with brass plating
The major difference between brass plating and electroplated gilding lies in the material that is used to finish the object.
In the case of brass plating, copper is used while gold or silver is used for galvanic gilding.
Certainly galvanic gilding allows for a better aesthetic result, greater luxury, and superior wear resistance than brass-plated objects that can easily oxidize, but the price is much higher than brass-plating and the process is much longer.
With brass plating, on the other hand, an inexpensive result can be achieved, which is precisely why it is often chosen especially when applied to everyday objects. If, on the other hand, we are dealing with valuable objects then opting for electroplated gilding is definitely the best choice.
How does the process take place?
The oxide that is formed is not due to material input but to a transformation of the original surface of the object. The aluminum surface undergoing anodizing is progressively oxidized from the outside of the surface progressing inward. The ‘oxide that is formed has a larger volume than the original metal (aluminum) so that apparently, from a dimensional point of view, it seems away is a material contribution, in reality the thickness of oxide partly “penetrates” into the metal partly “grows” outward. In practice for a thickness of e.g. 10 microns, 5 microns penetrated and 5 microns expanded so the geometric increase amounts to 5 microns. Note that, on a diameter, the 10-micron thickness produces an increase in diameter of 10 microns, not 20.
Oxide also tends to form fairly uniformly in recesses, undercuts, and inside pipes. The structure of the oxide is very similar to the “honeycomb” structure with vertical tubules with respect to the thickness formed. These tubules are much less than a micron in diameter, but particular dyes can penetrate them, being able to impart a wide variety of colorations to the oxide layer. Following the formation of the oxide layer and, eventual staining, a pore-closing operation is performed in order to ensure compactness and corrosion resistance. This operation is called fixing and can be done cold or hot. in any case the pores are closed, however, it turns out to be safer to heat fix especially for colored oxide layers.
Treatable materials
- Iron
- Inox brass
- Copper
- Zama
Regulations
- Small parts can be conveniently processed in rotobarrel.
- Any customer specifications..
Possible finishes
- White (neutral)
- Black
- Blue
- Red
Maximum treatable size
500 x 250 x 800 mm
Treatable materials
- Iron
- Inox brass
- Copper
- Zama
Possible finishes
- White (neutral)
- Black
- Blue
- Red
Regulations
- Small parts can be conveniently processed in rotobarrel.
- Any customer specifications.
Maximum treatable size
500 x 250 x 800 mm
Sectors
implementing
implementing
Application areas
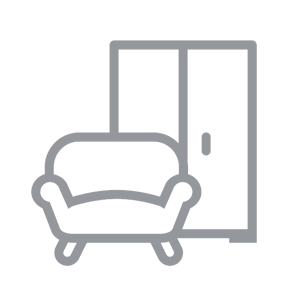
Furniture
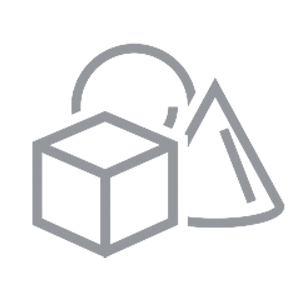
Objects
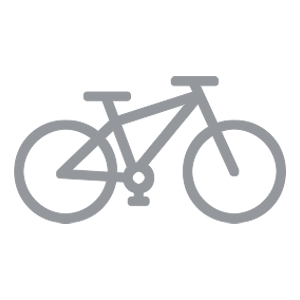
Cycle
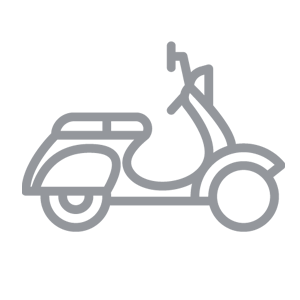