Decorative treatments
Nickel plating
Decorative treatments
Nickel plating
Decorative treatments: electroless nickel plating
Electroless nickel plating is a plating process in which a layer of nickel is deposited on a metal surface by the application of electric current. This treatment offers many advantages and is widely used in various industries.
The main characteristics of electroless nickel plating include corrosion resistance, aesthetic appearance, hardness, and the ability to improve the sliding and wear properties of treated surfaces. Nickel is a highly corrosion-resistant metal, so its electrolytic deposition provides effective protection against oxidation and rust, extending the life and durability of components.
In addition, electroless nickel plating offers a wide range of surface finishes, ranging from bright to satin or matte nickel, allowing the desired appearance to be achieved for specific applications. This aesthetic versatility makes electroless nickel plating ideal for components that require a high-quality finish, such as jewelry, furniture accessories, kitchenware, and automotive parts.
Another advantage of electroless nickel plating is its ability to improve the mechanical properties of treated surfaces. Nickel can increase the hardness of the base material, reduce friction and improve wear resistance. These features are particularly useful in applications where surfaces are subject to mechanical stress or must slide over each other with minimal friction, such as in the case of machine parts and industrial equipment.
In summary, electroless nickel plating is a versatile and advantageous process for protection, aesthetics, and improvement of mechanical properties of metal surfaces. Its widespread use in various industries testifies to the importance and effectiveness of this finishing treatment.
How does the galvanic bath work?
Galvanic bath is an electrochemical process used for the deposition of a layer of metal on a metal surface. In this process, the surface to be treated, called the cathode, is immersed in an electrolyte solution containing metal ions, while an anode consisting of the metal to be deposited is connected to the power supply.
When an electric current is applied, metal ions in the electrolyte solution are reduced at the cathode surface, forming a metal layer that is deposited on it. The anode, on the other hand, slowly wears out due to oxidation and loss of metal ions.
The electroplating bath requires precise control of parameters, such as electric current, temperature and chemical composition of the electrolyte solution, in order to achieve a uniform, high-quality metal layer. The deposition time may vary depending on the desired layer thickness and the specific characteristics of the application.
This process is widely used for plating metals such as gold, silver, copper, nickel, chromium, and zinc, enabling the aesthetic, protective, and functional properties of metal surfaces to be improved. The electroplating bath has applications in a variety of industries, including the automotive industry, goldsmithing, electronics and general manufacturing.
How does chemical nickel plating take place?
Chemical nickel plating, also known as chemical nickel deposition (DCN), is a plating process in which the nickel layer is deposited on a metal surface by a chemical reaction rather than the application of electric current. During the process, the metal surface is immersed in a chemical solution containing nickel salts and other reagents. The chemical reaction causes the reduction of nickel salts on the metal surface, allowing the nickel to deposit evenly. Chemical nickel plating is used for applications requiring precise control of nickel layer thickness and for protection against corrosion, abrasion and wear.
What is the difference between electrolytic or chemical nickel plating
The main difference between electroless and chemical nickel plating lies in the process of deposition of the nickel layer on the metal surface. In electroless nickel plating, nickel is deposited through the application of electric current, while in chemical nickel plating, the nickel layer is formed through a chemical reaction without the use of electric current. Electroless nickel plating offers greater control over the thickness and uniformity of the deposited layer, as well as advantages such as corrosion resistance and improved adhesion. On the other hand, chemical nickel plating can be used to deposit nickel layers on complex or nonconductive surfaces, allowing greater versatility in the plating process. Both methods have their specific applications depending on the needs of the industry and the characteristics of the material being processed.
How to Nickel Aluminum?
Nickeling aluminum can be a complex process because of the reactive nature of aluminum. However, there are several methodologies to achieve good adhesion of nickel on the surface of aluminum. One common technique is the use of a chemical primer or alkaline solution to prepare the aluminum surface before nickel plating. This helps remove oxide and improve nickel adhesion. Next, the aluminum is immersed in an electrolytic nickel bath, where an electric current is applied to deposit the nickel layer on the aluminum surface. It is important to maintain a controlled temperature and current during the process to achieve a uniform, high-quality deposit. Aluminum nickel plating requires specialized skills and is best done by professionals or companies that specialize in metal plating.
DIY nickel plating, can I operate on my own?
Nickel plating is a complex process that requires specialized skills and specific equipment to be performed properly. Although it is possible to find do-it-yourself nickel-plating kits on the market, it is important to understand that operating on your own carries risks and limitations. Handling the chemicals and acids used in the process require strict safety precautions, as they can be toxic or corrosive. In addition, controlling critical parameters such as temperature, pH and electric current requires in-depth knowledge. It is advisable to outsource nickel plating to experienced professionals who have the proper equipment and are familiar with safety procedures to ensure quality results and minimize health and environmental risks.
How does the process take place?
Nickel-plating plants are lines composed of tanks where the objects to be nickel-plated are moved by fast overhead cranes following predetermined cycles that depend on the type of material to be nickel-plated and, with the same material, the surface condition of the material.
The tanks contain chemicals in an aqueous solution where at predetermined temperatures, dwell times, and possible current densities, degreasing operations are carried out,to remove the inevitable oils and greases from the mechanical processing previously performed on the parts. Pickling is done to remove oxides and activations are performed to make surfaces suitable for nickel deposition. The nickel plating tank (electrolytic cell) contains the nickel salts with all the additives and the nickel metal (anodes), which with the passage of the electric current will go into solution and form the nickel deposit on the objects to be coated. All physical parameters of the process are automatically controlled, the concentrations of all products in the various tanks are continuously reset according to the treated surface (flowing current) or on chemical analysis carried out at predetermined and updated frequencies.
Decorative treatments: electroless nickel plating
Electroless nickel plating is a plating process in which a layer of nickel is deposited on a metal surface by the application of electric current. This treatment offers many advantages and is widely used in various industries.
The main characteristics of electroless nickel plating include corrosion resistance, aesthetic appearance, hardness, and the ability to improve the sliding and wear properties of treated surfaces. Nickel is a highly corrosion-resistant metal, so its electrolytic deposition provides effective protection against oxidation and rust, extending the life and durability of components.
In addition, electroless nickel plating offers a wide range of surface finishes, ranging from bright to satin or matte nickel, allowing the desired appearance to be achieved for specific applications. This aesthetic versatility makes electroless nickel plating ideal for components that require a high-quality finish, such as jewelry, furniture accessories, kitchenware, and automotive parts.
Another advantage of electroless nickel plating is its ability to improve the mechanical properties of treated surfaces. Nickel can increase the hardness of the base material, reduce friction and improve wear resistance. These features are particularly useful in applications where surfaces are subject to mechanical stress or must slide over each other with minimal friction, such as in the case of machine parts and industrial equipment.
In summary, electroless nickel plating is a versatile and beneficial process for protection, aesthetics, and improvement of mechanical properties of metal surfaces. Its widespread use in various industries testifies to the importance and effectiveness of this finishing treatment.
How does the galvanic bath work?
Galvanic bath is an electrochemical process used for the deposition of a layer of metal on a metal surface. In this process, the surface to be treated, called the cathode, is immersed in an electrolyte solution containing metal ions, while an anode consisting of the metal to be deposited is connected to the power supply.
When an electric current is applied, metal ions in the electrolyte solution are reduced at the cathode surface, forming a metal layer that is deposited on it. The anode, on the other hand, slowly wears out due to oxidation and loss of metal ions.
The electroplating bath requires precise control of parameters, such as electric current, temperature, and chemical composition of the electrolyte solution, in order to achieve a uniform, high-quality metal layer. The deposition time may vary depending on the desired layer thickness and the specific characteristics of the application.
This process is widely used for plating metals such as gold, silver, copper, nickel, chromium, and zinc, enabling the aesthetic, protective, and functional properties of metal surfaces to be improved. The electroplating bath has applications in a variety of industries, including the automotive industry, goldsmithing, electronics and general manufacturing.
How does chemical nickel plating take place?
Chemical nickel plating, also known as chemical nickel deposition (DCN), is a plating process in which the nickel layer is deposited on a metal surface by a chemical reaction rather than the application of electric current. During the process, the metal surface is immersed in a chemical solution containing nickel salts and other reagents. The chemical reaction causes the reduction of nickel salts on the metal surface, allowing the nickel to deposit evenly. Chemical nickel plating is used for applications requiring precise control of nickel layer thickness and for protection against corrosion, abrasion and wear.
What is the difference between electrolytic or chemical nickel plating
The main difference between electroless and chemical nickel plating lies in the process of deposition of the nickel layer on the metal surface. In electroless nickel plating, nickel is deposited through the application of electric current, while in chemical nickel plating, the nickel layer is formed through a chemical reaction without the use of electric current. Electroless nickel plating offers greater control over the thickness and uniformity of the deposited layer, as well as advantages such as corrosion resistance and improved adhesion. On the other hand, chemical nickel plating can be used to deposit nickel layers on complex or nonconductive surfaces, allowing greater versatility in the plating process. Both methods have their specific applications depending on the needs of the industry and the characteristics of the material being processed.
How to Nickel Aluminum?
Nickeling aluminum can be a complex process because of the reactive nature of aluminum. However, there are several methodologies to achieve good adhesion of nickel on the surface of aluminum. One common technique is the use of a chemical primer or alkaline solution to prepare the aluminum surface before nickel plating. This helps remove oxide and improve nickel adhesion. Next, the aluminum is immersed in an electrolytic nickel bath, where an electric current is applied to deposit the nickel layer on the aluminum surface. It is important to maintain a controlled temperature and current during the process to achieve a uniform, high-quality deposit. Aluminum nickel plating requires specialized skills and is best done by professionals or companies that specialize in metal plating.
DIY nickel plating, can I operate on my own?
Nickel plating is a complex process that requires specialized skills and specific equipment to be performed properly. Although it is possible to find do-it-yourself nickel-plating kits on the market, it is important to understand that operating on your own carries risks and limitations. Handling the chemicals and acids used in the process require strict safety precautions, as they can be toxic or corrosive. In addition, controlling critical parameters such as temperature, pH and electric current requires in-depth knowledge. It is advisable to outsource nickel plating to experienced professionals who have the proper equipment and are familiar with safety procedures to ensure quality results and minimize health and environmental risks.
How does the process take place?
Nickel-plating plants are lines composed of tanks where the objects to be nickel-plated are moved by fast overhead cranes following predetermined cycles that depend on the type of material to be nickel-plated and, given the same material, its surface condition.
The tanks contain chemicals in an aqueous solution where at predetermined temperatures, dwell times, and possible current densities, degreasing operations are carried out to remove the unavoidable oils and greases from the mechanical processing previously performed on the parts. Pickling is done to remove oxides and activations are performed to make surfaces suitable for nickel deposition. The nickel plating tank (electrolytic cell) contains the nickel salts with all the additives and the nickel metal (anodes), which with the passage of the electric current will go into solution and form the nickel deposit on the objects to be coated. All physical parameters of the process are automatically controlled, the concentrations of all products in the various tanks are continuously reset according to the treated surface (flowing current) or on chemical analysis carried out at predetermined and updated frequencies.
Treatable materials
- Stainless steel, AISI 316, AISI 304, AISI 303
- Carbon steel, iron, C40, C45, AVP, AVZ
- Aluminum, cast aluminum, 2011, 11S, 6060, 6082, 7075, Anticorodal, Ergal
- Brass, copper
- Sintered
- Zama
Regulations
- UNI ISO 1458
- UNI 5342
Treatable materials
- Stainless steel, AISI 316, AISI 304, AISI 303
- Carbon steel, iron, C40, C45, AVP, AVZ
- Aluminum, cast aluminum, 2011, 11S, 6060, 6082, 7075, Anticorodal, Ergal
- Brass, copper
- Sintered
- Zama
Regulations
- UNI ISO 1458
- UNI 5342
Maximum treatable size
Aluminum, Zamak , Iron, Brass/Copper, Stainless steel:
2,700 x 500 x 1,200 mm
Maximum treatable size
Aluminum, Zamak , Iron, Brass/Copper, Stainless steel:
2,700 x 500 x 1,200 mm
Sectors
implementing
implementing
Application areas
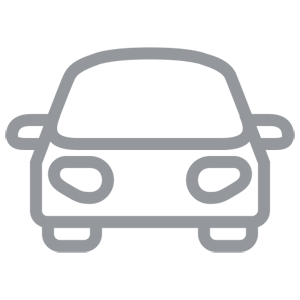
Automotive
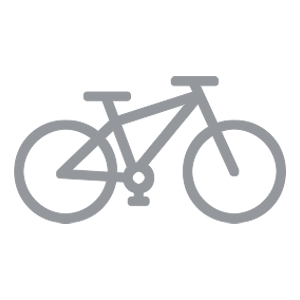
Cycle
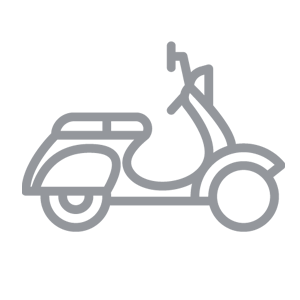
Motorcycle
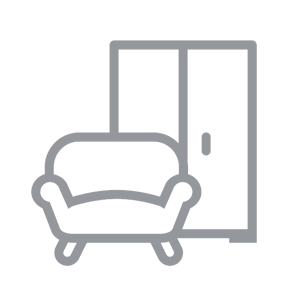
Furniture
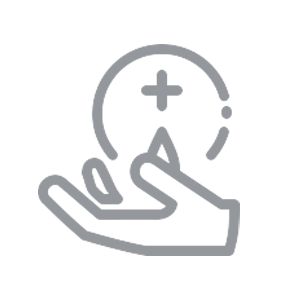
Hydrosanitary
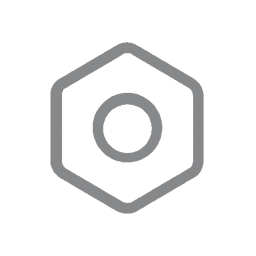
Minutery
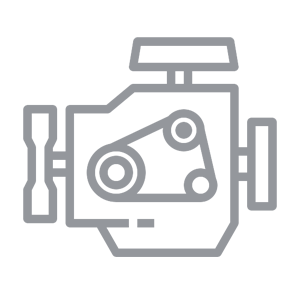